06. dubna 2016 00:23
Aspekty energetické účinnosti obráběcích strojů
V mnoha průmyslových oblastech se dnes stále více diskutuje o efektivním využívání energie. Obráběcí stroje obsahují celou řadu pohonů a pomocných agregátů, jejichž spotřeba energie může během obrábění silně kolísat. Například pohon hlavního vřetena a systém dodávky chladicího média pracují během hrubování s velkým odběrem materiálu blízko jmenovitého provozního bodu, zatímco odběr energie během obrábění načisto je výrazně nižší. Propojení jednotlivých komponent a agregátů obráběcího stroje s aspekty produktivity a kvality je velmi těsné. Z hlediska detailního posouzení výrobních procesů až po příkon jednotlivých spotřebičů lze vyhodnotit potenciální úspory a definovat opatření pro efektivní využití energie.
V mnoha odvětvích investičního průmyslu se energetická účinnost stává významnou charakteristikou produktu. Proto jsou hnací motory technických dopravních zařízení již dlouhou dobu rozděleny podle tříd účinnosti. Formulace pro zvyšování energetické účinnosti při výrobě s obráběcími stroji jsou velmi různorodé. Potenciální úspory vyplývají ze vztahu k základnímu zatížení obráběcích strojů, které i v nevýrobních fázích znamená určitý odběr energie. Základní zatížení rozhodujícím způsobem určují pomocné agregáty stroje. Vedle použití energeticky účinných motorů v pomocných agregátech existují možnosti snížení základního zatížení pomocí energetického managementu. Spotřebiče v neproduktivní fázi jsou přitom cíleně deaktivovány řízením stroje.
Opatření pro podporu obsluhy během seřizování rovněž zlepšují energetickou účinnost, protože jsou zkracovány neproduktivní fáze, a tím se zmenšuje vliv základního zatížení na celkovou energetickou bilanci. Zmetky nevyhnutelně zvyšují energetické nároky na dobrý dílec. Přesnost od vyrobení prvního dílce tak může být rozhodujícím faktorem energetické účinnosti obráběcího stroje. Koncepce stroje s vyváženou tepelnou charakteristikou a přesnou polohovací mechanikou přitom mají jasnou výhodu.
Příkon při frézování
Příkon procesu frézování se rozděluje na skupiny spotřebičů:
- příprava chladicího maziva,
- výroba stlačeného vzduchu,
- elektricky napájené pomocné agregáty frézky, jako řídicí jednotka,
- CNC s hlavním vřetenem a pohony posuvu.
K tomu přistupuje započitatelný podíl energie pro osvětlení, větrání a klimatizaci výrobní haly. Příkon frézky silně závisí na její velikosti a na aktuální úloze obrábění.
Ve sledovaném příkladu se provádí frézování hliníkového pouzdra o rozměrech 150 mm × 50 mm × 25 mm na obráběcím centru s rozměry pracovního prostoru 850 mm × 700 mm × 500 mm. Celková střední spotřeba všech výše uvedených skupin spotřebičů činí při hrubování 13 kW a při obrábění načisto 7,4 kW. Bližší informace o rozdělení spotřeby energie na jednotlivé skupiny spotřebičů poskytují bilance výkonu při hrubování a obrábění načisto.
Chladicí mazivo se připravuje centrálně, mimo frézku (čerpání, temperování). Spotřeba činí při hrubování průměrně 5,1 kW. Při obrábění načisto se průměrný příkon snižuje na 1,5 kW. V době přípravy k výrobě je příkon prakticky nulový. Suché obrábění nabízí velký potenciál pro zvýšení energetické účinnosti a efektivity zdrojů. U mnoha frézovacích aplikací však může odpadnutí chladicího maziva vést ke zřetelnému zvýšení zmetkovitosti, a tím i ke zhoršení energetické bilance.
Střední spotřeba stlačeného vzduchu se ve fázích připravenosti k výrobě, hrubování a obrábění načisto mění jen nepatrně a činí v průměru cca 1,3 kW. Stlačený vzduch se používá pro obrábění s minimálním množstvím mazání, při výměně nástrojů jakož i pro čištění obrobku a v malém množství také k proplachování vzduchem (vřeteno, proměřování nástroje, měřidla délky). K elektrickým spotřebičům stroje náleží, kromě CNC řízení s hlavním vřetenem a pohony posuvu, četné pomocné agregáty (výměník palet, chlazení, hydraulika, automatizace). Příkon pomocných agregátů se v provozních režimech připravenosti k výrobě, hrubování a obrábění načisto mění pouze o 600 W. Při příkonu 2,5 kW určují pomocné agregáty významně spotřebu energie v režimu připravenosti k výrobě.
Deaktivace pomocných agregátů podle potřeby zde proto nabízí významný potenciál. CNC řízení se všemi posuvovými motory a hlavním vřetenem potřebuje ve sledovaném případě jak při hrubování, tak při obrábění načisto právě 27 % celkového výkonu. Střední výkon pohonů posuvu činí v obou případech asi 250 W a je rozhodujícím způsobem určován přídržnou silou svislé osy. Pouze během zrychlování a zpomalování se krátkodobě vyskytují špičkové hodnoty.
Energetická účinnost komponent pohonu
Hlavní vřeteno a pohony posuvu patří k hlavním komponentám obráběcího stroje. Energetická účinnost hnacích komponent závisí na poměru vydaného a odebraného výkonu a odráží se tak ve stupni účinnosti. Skupina pohonů obráběcího stroje převádí odebíranou elektrickou energii na odevzdávaný mechanický výkon. Do skupiny pohonů náleží napájecí modul, moduly pohonu, motory a mechanické komponenty. Údaje o stupni účinnosti se typicky vztahují na jmenovitý provozní bod. V jiných provozních bodech se může stupeň účinnosti jednotlivých komponent výrazně lišit. Napájecí a pohonné moduly HEIDENHAIN dosahují stupně účinnosti přes 95 %.
Příkon při frézování
Příkon hlavního vřetena a pohonů posuvu je rozčleněn pro dva typy obrábění.
Příklad 1: Čelní hrubování
Při čelním hrubování s posuvem rovnoběžným s osou odebírají motory posuvu průměrně pouze 200 W. Hlavní vřeteno dosahuje s cca 19 kW svého jmenovitého výkonu.
Příklad 2: Kruhová kapsa
Kruhová kapsa se obrábí jedním hrubovacím a jedním dokončovacím cyklem. Střední výkon pohonů posuvu zde činí 100 W. Hlavní vřeteno potřebuje výkon 1,5 kW.
Shrnutí
Pohony posuvu mají pouze malý podíl na celkovém výkonu CNC systému a mohou tedy energetickou účinnost jen nepatrně zvýšit. Citelný vliv na energetickou bilanci může naproti tomu mít volba hlavního vřetena. Jestliže pohon hlavního vřetena pracuje hluboko pod jmenovitým provozním bodem, zvyšují se vlastní ztráty pohonu s negativními důsledky na energetickou bilanci. Pokud hlavní vřeteno omezí maximální možný odběr materiálu frézovacího procesu, bude tento proces nevyhnutelně trvat déle. Důsledek: kvůli základnímu zatížení, generovanému pomocnými agregáty, bude energetická účinnost horší. Potenciálem pro účinnější formu frézovacích procesů je rovněž zohlednění stupně účinnosti vřetenových motorů, například použitím synchronního místo asynchronního motoru.
Účinnost rekuperačních napájecích modulů
Jakékoli zrychlení některého pohonu vyžaduje na druhé straně zabrzdění. Přitom se energie pohybující se hmoty pohonů opět z větší části přemění na elektrickou energii. Napájecí moduly CNC řídicích systémů HEIDENHAIN se vyrábějí jak rekuperační, tak i bez rekuperace. V napájecím modulu bez rekuperace se kinetická energie, uvolněná během brzdění, přeměňuje v brzdových odporech na teplo. Rekuperační napájecí modul odvádí tuto energii zpět do rozvodné sítě. Rekuperační větev, která je k tomu zapotřebí, a komponenty nutné pro vyhlazení síťového napětí však produkují ztráty i tehdy, když pohony nepotřebují žádný výkon.
Ztrátový výkon se nepatrně zvyšuje i během normálního napájení. Rekuperační napájecí modul pracuje účinněji než modul bez rekuperace tehdy, když rekuperovaná energie převažuje nad ztrátovým výkonem. Rozhodnutí o použití rekuperačního napájecího modulu nebo modulu bez rekuperace tak závisí na tom, jaká obrábění na stroji očekáváme.
Pro energetickou bilanci je důležitý počet výměn nástrojů. V jednom příkladu je frézování s výkonem 15 kW cyklicky přerušováno výměnou nástrojů. Náběh hlavního vřetena vyžaduje špičkový výkon cca 60 kW. Zatímco rekuperační napájecí modul odvádí během brzdění krátkodobě do sítě 48 kW, modul bez rekuperace převádí kinetickou energii na teplo.
Vzhledem k vysokému řeznému výkonu klesá střední vstupní výkon, čím častěji je frézování přerušováno kvůli výměně nástrojů. Rekuperační napájecí modul přitom pracuje účinněji, jakmile je časový odstup mezi dvěma výměnami nástrojů kratší než 100 s (což odpovídá 0,6 výměnám nástrojů za minutu). V procesech s mnoha výměnami nástrojů za minutu se rekuperační napájecí modul většinou osvědčuje jako lepší volba. Při obrysovém frézování, kdy zřídka dochází k výměně nástrojů, jsou přednosti na straně systému bez rekuperace.
Cílená deaktivace pomocných agregátů
Porovnání příkonu dvou obráběcích center (BAZ) a jedné výrobní linky se třemi obráběcími stanicemi znovu ozřejmuje potenciály: vzhledem k tomu, že se energetické nároky některých skupin spotřebičů ve fázi připravenosti k výrobě snižují jen nepodstatně, je nutno udržovat neproduktivní fáze co nejkratší. U obráběcích center pro malé výrobní dávky lze energetickou bilanci cílenou deaktivací pomocných agregátů významně zlepšit. Nadto vyplývají další potenciály úspor použitím energeticky úsporných čerpadel v okruhu chladicího maziva.
Důsledné vypínání pomocných agregátů (hydraulika, chlazení vřetena) nebo dodávky stlačeného vzduchu však může mít i opačný účinek. Jestliže nárazová absence odpadního tepla pomocných agregátů nebo temperující působení médií vede k tepelným deformacím rámu stroje, mohou vznikat zmetky, které zhoršují energetickou bilanci výrobního procesu. Pomocné agregáty tedy lze cíleně vypínat zejména u strojů s nízkým sklonem k tepelným deformacím. V každém případě je předpokladem pečlivý návrh koncepce úspory energie.
CNC systém přitom lze použít jako centrální řídicí jednotku energetického managementu obráběcího stroje a příslušných periferií. V systému iTNC 530 jsou proto k dispozici speciální PLC funkce k provázání událostí ve výrobním procesu (např. NC stop) s výstupy pro ovládání pomocných agregátů. Událostem lze přiřadit doby prodlevy, takže například pohony jsou po určité době nečinnosti zablokovány a odpojeny od napájení. Na tomto základu je možno vytvořit funkce pro deaktivaci různých pomocných agregátů, os, osvětlení výrobního prostoru atd. Tyto základní funkce mohou být vytvořeny výrobcem stroje dle vlastního přání a přizpůsobeny danému typu stroje. Pro uživatele je nápomocné další zapouzdření, v němž lze energetický management přizpůsobit daným zvyklostem použití. V uvedeném příkladu lze deaktivační funkce (pohony, blokování, pohotovostní režim, nouzové vypnutí, odpojení) konfigurovat pro různé provozní režimy.
Zkrácení vedlejších časů optimální podporou při seřizování
Vzhledem k relativně vysokému energetickému základnímu zatížení obráběcích strojů mají vedlejší časy rozhodující vliv na energetickou účinnost procesu obrábění. Pro snížení energetických nároků na dílec by měly být vedlejší časy, jako je příprava nebo seřizování, co nejkratší. V principu platí: efektivní je to, co zvyšuje produktivitu stroje.
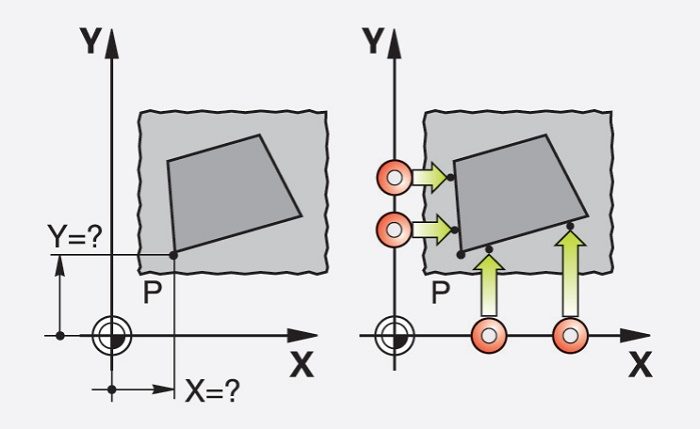
Časová úspora
Pro tento způsob ustavení polotovaru s dotykovou sondou TS společnosti HEIDENHAIN představuje úspora času 4 min, resp. cca 72 %.
Úspora energie
Při 10 ustaveních polotovaru za den a 220 pracovních dnech se ušetří 580 kWh za rok. To přibližně odpovídá roční spotřebě
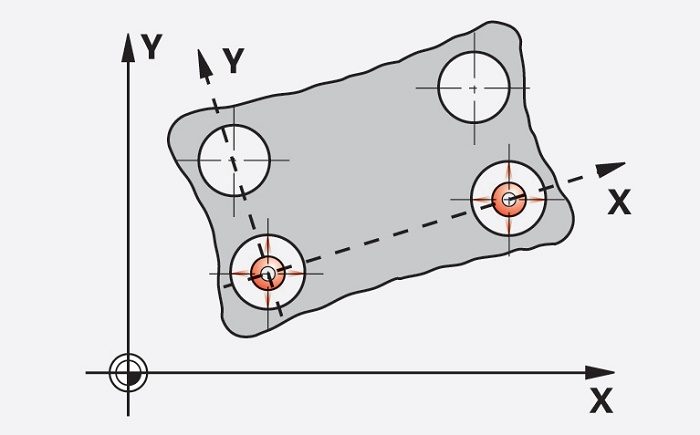
Časová úspora
Pro tento způsob ustavení polotovaru s dotykovou sondou TS společnosti HEIDENHAIN představuje úspora času 5 min, resp. cca 77 %.
Úspora energie
Při 10 ustaveních polotovaru za den a 220 pracovních dnech se ušetří 730 kWh za rok. To přibližně odpovídá roční spotřebě energie 6 chladniček s energetickou účinností A++.
Vedlejší časy při seřizování
Povely NC programu se vztahují ke vztažným bodům obrobku, které musí být nejdříve zjištěny při upínání obrobku. Rychlého a bezpečného zjištění vztažných bodů lze dosáhnout pomocí dotykové sondy obrobku. Předdefinované snímací cykly a bezporuchové propojení dotykové sondy s řídicím systémem výrazně šetří vedlejší časy a současně zvyšují přesnost obrábění. V kombinaci se snímacími funkcemi TNC řídicích systémů lze s dotykovými sondami TS společnosti HEIDENHAIN automaticky nastavit vztažné body. Tím lze zamezit chybám při seřizování, které nutně vedou ke zmetkům.
Dotykové sondy snižují vedlejší časy, zlepšují kvalitu výroby, zamezují zmetkům a zvyšují produktivitu. Díky tomu klesá energetická náročnost na zhotovený dílec. Potenciály úspory vedlejších časů jsou vysvětleny na dvou příkladech. Jsou přitom porovnány přípravné časy s použitím indikátorových hodinek a dotykové sondy HEIDENHAIN na obráběcím stroji se základním zatížením 4 kW.
Úloha 1
- Vyrovnat polotovar rovnoběžně s osami
- Určit vztažný bod na jednom rohu v rovině obrábění
- V ose nástroje definovat vztažný bod na povrchu polotovaru
Úloha 2
- Vyrovnat polotovar rovnoběžně s osami pomocí dvou děr
- Určit vztažný bod uprostřed první díry v rovině obrábění
- V ose nástroje definovat vztažný bod na povrchu polotovaru
Měřicí systémy pro energeticky účinný provoz regulovaných pohonů
V regulačních obvodech motorů hlavního vřetena a os posuvu s přímým pohonem mohou již nepatrná rušení zpětnovazebních signálů vést k velkému kolísání proudu motoru.
Při interpolaci signálů snímače polohy vznikají v rámci jedné periody signálu krátkoperiodické odchylky (interpolační odchylky), které činí typicky 0,5% periody signálu. S narůstající frekvencí interpolačních odchylek již nemůže pohon posuvu sledovat průběh chyby. Prostřednictvím interpolačních odchylek jsou však generovány dodatečné proudové komponenty. Při stejném krouticím momentu následně stoupá odběr motoru a zhoršuje se stupeň účinnosti. Dodatečně odebíraná energie se mění na teplo. Toto teplo musí být typicky odváděno chlazením motoru, a tedy i s dodatečnou spotřebou energie.
Při porovnání vlivu optického úhlového snímače a vestavěného magnetického úhlového snímače na otočném stole s přímým pohonem vyniká význam vysoce kvalitních polohových signálů. Použitý úhlový snímač typu RCN 226 se 16 384 dílky vytváří sotva vnímatelné poruchy motorového proudu a motor vyvíjí málo tepla. Vestavěný úhlový snímač disponuje díky magnetickému snímání zřetelně menším počtem signálních period. Při shodném nastavení regulátoru vznikají značné poruchy motorového proudu. Například při otáčkách cca 30 min–1 je efektivní hodnota proudu o 15 A vyšší než v případě optického úhlového snímače. Důsledkem je výrazně vyšší zahřívání motoru.
Použitím úhlového snímače s nižší jakostí signálu mohou vzniknout větší ztráty motoru. Kromě toho je nutno v energetické bilanci zohlednit dodatečné energetické nároky aktivního chlazení. Pro zlepšení energetické účinnosti motoru by proto měly být použity úhlové snímače s vysokou kvalitou signálu.
Minimalizace zmetků pomocí technologie uzavřené smyčky
Zmetky snižují produktivitu výrobního procesu, a tak významně přispívají k růstu energetických nákladů na hotový dobrý dílec. Významnou příčinou produkce zmetků jsou tepelné deformace posuvových os, založených na kuličkových šroubech. V závislosti na rychlostech a silách posuvu se může rozložení teplot na kuličkových šroubech velmi rychle měnit.
Změny délky, které přitom vznikají (typicky: 100 μm/m během 20 min), mohou u obráběcích strojů s polouzavřenou smyčkou (bez měřidel délky, Obrázek 1) vést k významným chybám na obrobku. Když je pro zjištění polohy saní použito měřidlo délky (Obrázek 2), nemá zvýšení teploty kuličkového šroubu (Obrázek 3) na přesnost žádný vliv. Hovoříme o provozu v uzavřené smyčce, protože chyby mechaniky pohonu v regulačním obvodu polohy jsou měřeny, a tedy kompenzovány.
Příklad obrábění: ovládací páka stabilizační plochy
Pro vyhodnocení přesnosti při výrobě malých dávek je ovládací páka obrobena dvakrát ze stejného polotovaru. Druhý obrobek se přitom frézuje s posunutím o pouhých 10 mm směrem dolů.
Mezi oběma obrobeními se provede dvacet obráběcích cyklů stejného dílce nad polotovarem. Při obrábění v polouzavřené smyčce se obě kontury obrobků vzájemně liší, což se projevuje jako hrana.
Toto posunutí mezi obrobky činí u polouzavřené smyčky 44 μm. Při použití měřidel délky v uzavřené smyčce žádná hrana nevznikne. Tímto způsobem lze zajistit reprodukovatelnou přesnost od prvního dílce.
Úspora energie v uzavřené smyčce:
Obrobení 22 ovládacích pák ve sledovaném příkladu trvá 2 hodiny. Rozteč dvou děr s odstupem 350 mm má přitom být vyrobena s tolerancí IT7, což odpovídá přípustné odchylce ± 28 μm. Pro bezpečné dodržení tolerance IT7 při výrobě 22 dobrých dílců musí stroj v polouzavřené smyčce především 25 minut cyklicky zpracovat NC program. Odběr energie při zahřívání je pouze o cca 10 % menší, než při frézování. Náklady za energii na výrobu jednoho dobrého dílce v polouzavřené smyčce jsou tak o 19 % vyšší než při výrobě 22 dílců v uzavřené smyčce s měřidly délky. Bude-li se denně vyrábět 50 dílců v polouzavřené smyčce s předběžnou fází zahřívání, vznikne pro frézku s příkonem 8 kW při frézování během 220 pracovních dnů přídavný energetický nárok 660 kWh.
Shrnutí
Analýzy postupů třískového obrábění ukazují, že odběr CNC řízení, včetně pohonů posuvu a hlavního vřetena, často činí pouze 25 až 30 % celkového odběru. Pomocné agregáty ve stroji nebo v jeho okolí mají naproti tomu v energetické bilanci dominantní roli. Pro efektivní využití energie existuje řada možností. Významných úspor energie lze dosáhnout volbou komponent obráběcího stroje. V závislosti na výměnách nástrojů při frézování nebo výměně obrobků při soustružení může být smysluplný CNC řídicí systém s možností či bez možnosti rekuperace energie do síťového rozvodu. Rekuperovanou energii pak mají k dispozici spotřebiče v okolí stroje. Další možnosti úspory energie vyplývají z těsného přizpůsobení hlavních vřeten podmínkám obrábění stroje ve vztahu k otáčkám a krouticímu momentu. Pokud je požadováno univerzální dimenzování hlavního vřetena, může být motor vřetena provozován za nepříznivých podmínek – s odpovídajícími důsledky na energetickou bilanci.
Účinnost motorů hlavních vřeten a přímých pohonů lze citlivě ovlivňovat volbou snímačů polohy. Snímače s příliš nízkou citlivostí a přesností produkují v regulačním obvodu polohy vysoké proudové hodnoty. Pro dosažení vysoké účinnosti regulovaných pohonů jsou nezbytné snímače polohy s vysokým počtem impulsů. Měřidla délky prokazatelně zvyšují přesnost, a tím napomáhají dosáhnout přesnějšího a opakovatelnějšího výsledku obrábění. Tak lze rozhodujícím způsobem snížit zmetkovitost výroby a v přímém důsledku energetické nároky na jeden dobrý dílec. Dominantní podíl na celkovém odběru mají agregáty pro přípravu chladicích maziv, dodávku stlačeného vzduchu a hydrauliky, jakož i chlazení. Pokud je stroj vybaven účinnými pohony čerpadel, lze ušetřit značné množství energie. Kromě toho se nabízí energetický management, řízený CNC systémem, s cíleným vypínáním agregátů. Tak lze například po dokončení určité úlohy obrábění s daným časovým zpožděním vypnout pohony čerpadel. Potenciální úspory z hlediska energetických nároků lze často najít i ve vlastní výrobě.
Při relativně vysokém základním zatížení obráběcích strojů má redukce neproduktivních fází nejvyšší prioritu. CNC řídicí systémy společnosti HEIDENHAIN zde nabízejí mnoho způsobů podpory. Uživatelé mohou profitovat ze zkušeností nashromážděných po desítky let v oblasti třískového obrábění – počínaje koncepty uživatelsky přátelského programového obrábění přes funkce pro ustavování obrobků dotykovými sondami HEIDENHAIN po časově optimalizované a přesné řízení pohybu při tříosém a pětiosém obrábění.
Mohlo by se Vám líbit
Inteligentní šoupátko automaticky zajišťuje optimální otryskání a výrazně zlepšuje efektivitu nákladů
- Strojírenství
-
06. května 2024
Rösler PowerLine – první regulace průtoku tryskacího média na bázi AI4 Díky jedinečnému šoupěti Rösler PowerLine se tryskání metacími koly výrazně zjednodušuje. Nově vyvinuté inteligentní […]
OSTROJ roste a přijme desítky nových lidí. Zájem je hlavně o svářeče a zámečníky
- Práce
-
05. května 2024
Rostoucí opavská strojírenská firma OSTROJ plánuje v letošním roce přijmout přibližně 80 nových pracovníků. Společnost hledá zejména zkušené kandidáty na svářečské a zámečnické pozice, kterým chce […]
Kopřivnická Tatra získala dotaci na vývoj nákladního bateriového elektromobilu
- Automotive
-
03. května 2024
Automobilka Tatra Trucks se v posledních letech vedle produkce standardních nákladních vozidel intenzivně věnuje i vývoji automobilů s alternativními typy pohonů. Nedávno se jí podařilo […]