23. září 2016 00:35
Nové řešení termoplastových kompozitů pro snížení celkové hmotnosti karoserií a součástí automobilů
Jednou z hlavních hybných sil vývoje v automobilovém průmyslu je snižování emisí uhlíku. Výrobci a jejich partneři pro rozvoj pracují na více řešeních, která budou realizovat toto vylepšení – snižování aerodynamického odporu, umožnění elektrifikace a používání alternativních paliv. Většina výrobců automobilů vedle toho tvrdí, že modely automobilů, které přijdou na trh po roce 2021, musí být značně lehčí, až o několik set kilogramů na automobil.
Většina výrobců v tomto oboru má tendenci zvažovat používání ocelí s vysokou pevností a hliníku namísto kompozitů, protože kompozitní materiály jsou mnohem dražší. Když se na to podíváme z jiného pohledu, cena za úsporu hmotnosti (vyjádřeno v eurech za kilogram ušetřené hmotnosti) je příliš vysoká. Cena by byla standardně kolem 15–20 eur na kilogram dílu z karbonového kompozitu, což je podstatně více v porovnání s maximálním zvýšením, které by byl výrobce ochoten zaplatit (např. řešení z hliníku).
Společnost SABIC si je vědoma této výzvy a vyvinula nové formy cenově dostupných materiálů určené pro použití v procesu výroby dílů se zálisky (tzv. overmoulding). Tato technologie značně snižuje množství kompozitních materiálů, jak je znázorněno na obrázku 1. Na základě tohoto přístupu dochází k selektivnímu využití vysoce účinných multiaxiálních laminátů na bázi karbonových vláken s jednosměrnou strukturou (UD) podél hlavní zátěžové osy. Současně lze zapracovat funkční detaily, a tím ke snížení počtu jednotlivých výrobních kroků.
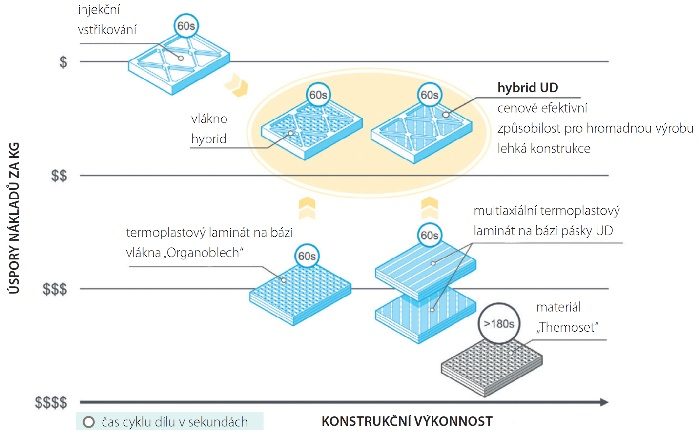
Obrázek 1: Optimalizace termoplastových kompozitů
Forma materiálu vyvinutá za tímto účelem, která se nejvíce hodí pro použití v automobilovém průmyslu, by byla multiaxiální laminát se stálou tloušťkou, jak je to znázorněno na obrázku 2.
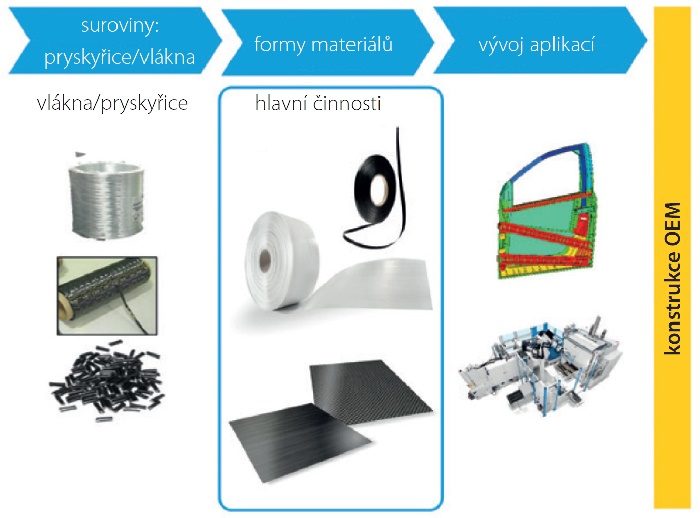
Obrázek 2: Nabídky řešení SABIC
Společnost SABIC vyvinula pásky UD složené z různých pryskyřic a vláken, multiaxiální lamináty nebo lamináty se strukturou jednosměrných vláken a dále může nabídnout širokou řadu kompatibilních produktů se zálisky. První pásky UD jsou uváděny pod názvem UDMAXTM GPP 45-70 TAPE, které jsou na bázi polypropylenu vyztuženého skelnými vlákny. Společnost SABIC může vedle toho poskytnout podporu při lisování a vývoji aplikací, což zahrnuje poskytnutí odborných zkušeností a schopnosti předvídat mechanické chování dílu.
Dále je třeba se zmínit, že společnost SABIC provádí vyhodnocení materiálů na bázi vláken, které mohou najít využití ve specifických aplikacích, jež nejsou předmětem tohoto článku.
Materiály
V závislosti na konkrétní aplikaci může dráha zatížení vést pouze jedním směrem. V tomto případě bude čistý laminát UD zaručovat maximální výkon, který bude mnohem vyšší, než by se dosáhlo u materiálů na bázi vláken. Například na obrázku 3 jsou znázorněny výsledky počátečního měření s porovnáním mechanických vlastností pásky UD a materiálu UD na bázi vláken s poměrem 80/20.
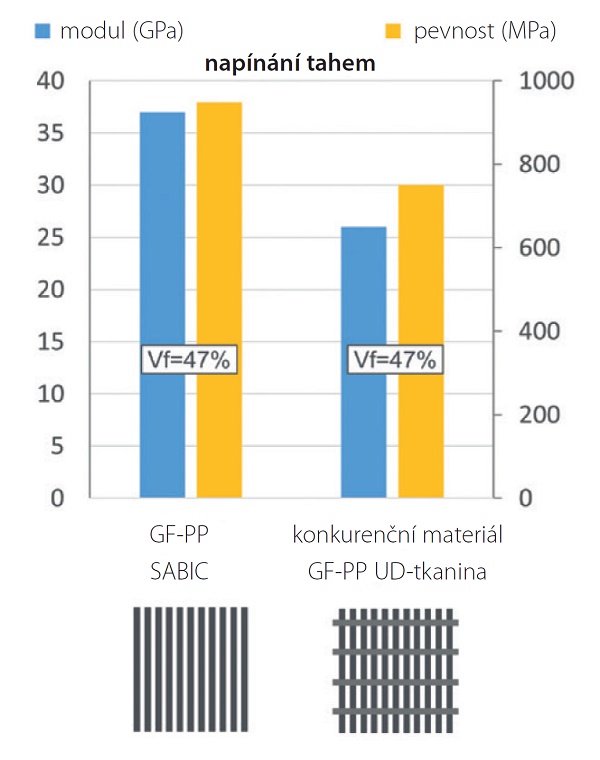
Obrázek 3: Porovnání vlastností pásky UD oproti tkanině
Materiály na bázi pásky UD mají současně velmi dobrý rozptyl vláken a impregnaci, která zaručuje výborné mechanické vlastnosti. To je zřejmé u pevnosti materiálu v tlaku, jak je to znázorněno na obrázku 4. V materiálech na bázi vláken zjevně dochází k vlnění vláken vyplývajícímu z jejich přirozených vlastností, což vede k nižším hodnotám pevnosti v tlaku.
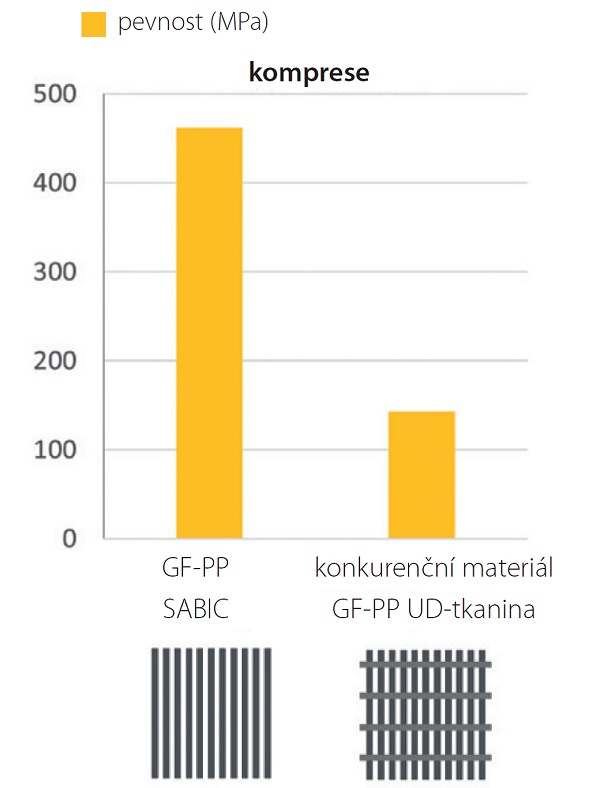
Obrázek 4: Pevnost v tlaku – páska UD oproti tkanině
Pevnost v tlaku by mohla být účelná u trámových struktur, které musí odolávat vysokému zatížení, například v případě havárií.
Další komponenty mohou být zatíženy v několika směrech. Studie prováděné na několika trámových podpěrných komponentech ukázaly, že typický laminát s optimalizovanou hmotností by měl obsahovat kombinaci směrových vrstev kladených v úhlu 0° a ±45°. V tomto případě nabízí UD materiály vyšší úspory hmotnosti v porovnání s tradičními materiály na bázi vláken, protože směry v úhlu 90° v tradičním materiálu s vlákny v úhlech 0/90° navyšují jen hmotnost a nepřispívá to ke zdokonalení struktury. Na obrázku 5 je příklad vypočtených vlastností laminátu na základě měřených údajů o tloušťce vrstvy. Aby byla dosažena stejná tuhost, řešení na bázi pásky UD by bylo o 26 % lehčí. Samozřejmě jsou také možná řešení, která představují kompromis mezi uvedenými možnostmi, například použití nekrčivých syntetických vláken (tzv. Non-Crimp Fabrics) jako imitace řešení na bázi pásky UD. Nicméně tyto typy materiálů vyžadují šití/tkaní a jejich impregnování je mnohem těžší. Tím se zvyšují náklady, aniž by došlo ke zlepšení funkčních vlastností díky použití čistého materiálu UD.
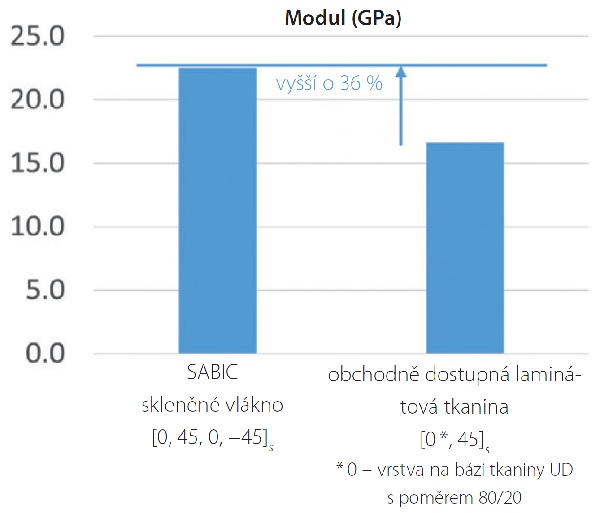
Obrázek 5: UD oproti tkanině, porovnání pro průměrný laminát
Příklady komponent
Studie optimalizace návrhu prováděné na různých komponentech mohou pomoci při vyhodnocení konkurenceschopnosti různých materiálů.
Návrh byl samostatně optimalizován s použitím oceli, hliníku, hořčíku (je-li to relevantní) a kompozitů ze skelných a uhlíkových vláken u určitých komponent se stejným rozsahem hodnot parametrů, pomocí stejného připevnění a se stejnými požadavky na tuhost/ pevnost/náraz. Jako příklad můžeme uvést příčný nosník u automobilu znázorněný na obrázku 6, který nese palubní desku, volant a několik komponent. Aplikace byla hliníková svařovaná konstrukce u stávajících modelů automobilů třídy C.
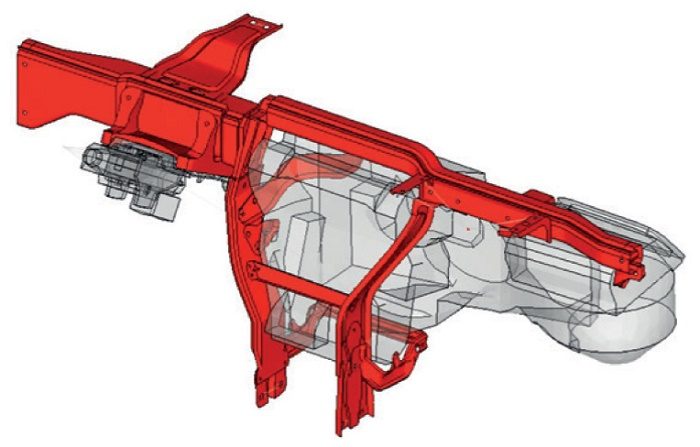
Obrázek 6: Referenční kovový příčný nosník
Většina automobilů ve stejné třídě by byla vyrobena z oceli. Pro tento díl byl vytvořen nový návrh s využitím technologie kompozitu se zálisky, který byl vyroben jako jednorázově tvářený komponent, jak je to znázorněno na obrázku 7.
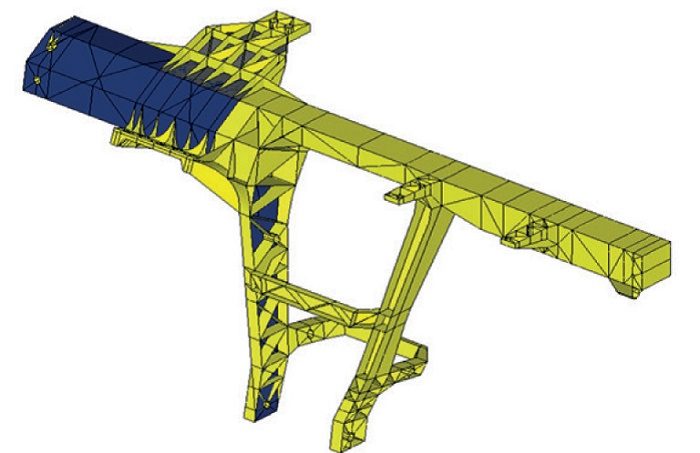
Obrázek 7: Kompozitní příčný nosník
I když může vypadat trochu odlišně, může být stále namontováno stejné zařízení. Modré části označují, kde jsou použity víceosé kompozitní lamináty, zatímco žluté části představují materiál se zálisky, v tomto případě materiál PP s dlouhými skelnými vlákny, který je o 30 % lehčí. Hlavním parametrem pro návrh tohoto dílu je vlastní frekvence vyvolaná vibracemi sloupku volantu. Kompozitní díl byl optimalizován na stejný výkon při 65 °C. I když tato teplota má sotva nějaký vliv na kompozitní materiál s nekonečným vláknem, má určitý vliv na materiál se záliskem.
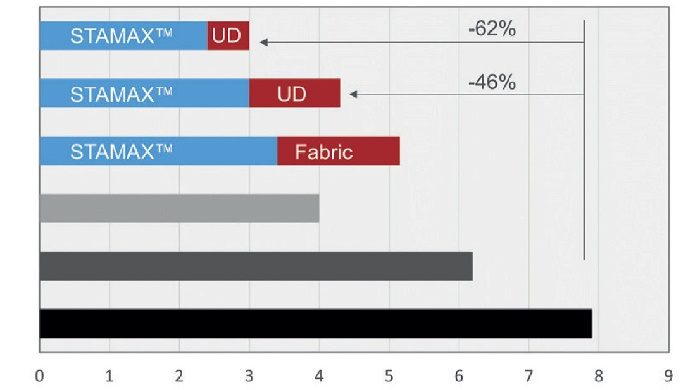
Obrázek 8:Hmotnosti příčných nosníků z různých materiálů
Modré segmenty na obrázku 8 označují množství materiálu vyrobeného se záliskem; červené segmenty množství materiálu na bázi nekonečných vláken. Z tohoto obrázku je jasně zřejmé, že termoplastový materiál s dlouhými vlákny (LFT) se zálisky představuje většinu materiálu. Tento materiál značně snižuje náklady na tento komponent.
V porovnání s řešením z oceli jsou možné úspory materiálu od čtyř do pěti kilogramů. Závisí to na volbě uhlíkových vláken nebo skleněných vláken. Z hlediska finanční úspory na kilogram hmotnosti je skelné vlákno výhodnější alternativou a je velmi dobře srovnatelné se snížením hmotnosti při použití hořčíku nebo hliníku. V tomto případě bychom mohli dokonce zvažovat používání uhlíkových vláken, protože množství potřebného materiálu je velmi malé.
Podívejme se na obdobnou studii prováděnou u bočních dveří automobilu, na něž jsou kladeny přísnější požadavky. Při návrzích pro tuto aplikaci jsou nejdůležitějšími parametry požadavky organizace Euro NCAP na odolnost vůči bočnímu nárazu, která byla ověřena při různých teplotách, v různých místech a s různými hodnotami rázového zatížení. Tím jsme získali pevné a bezpečné řešení při použití kompozitů. Referenční dveře byly nejmodernější ocelové dveře malých automobilů třídy B. Řešení s použitím kompozitů se skládá z konstrukčního řešení z dvou dílů (svařovaných dohromady), zatímco panel vnějších dveří u třídy A zůstává ocelový, jak je to znázorněno na obrázku 8. Červeně označená místa představují použití vícesměrných laminátů UD a šedě označená místa materiál se zálisky. Skutečné žebrování finálního optimalizovaného návrhu se liší, nicméně tento obrázek ukazuje hlavní koncepci. Další možnosti funkční integrace vnitřního panelu dveří ještě nebyly zváženy.
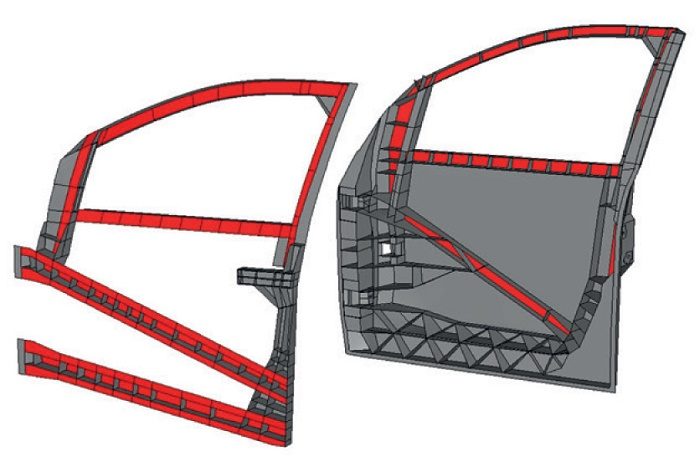
Obrázek 9: Kompozitní struktura bočních dveří
Výsledky jsou podobné jako u příčného nosníku u automobilu. Jedinou výjimkou je rozdíl mezi řešením z uhlíkových vláken a skleskleněných vláken, který nicméně není už tak velký. Je tomu tak, protože jednotlivé díly musí být navrhovány s vyšší pevností (náraz při havárii) než tuhostí. Takže velké prodloužení při přetržení je příznivé z hlediska zachování celistvosti nosníků při havárii.
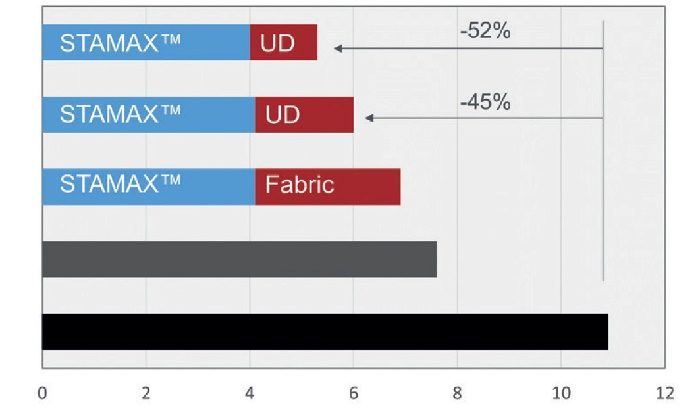
Obrázek 10: Hmotnosti bočních dveří z různých materiálů
Z toho vyplývá, že z hlediska nižší hmotnosti by řešení s použitím skelných vláken v porovnání s řešením z hliníku představovalo atraktivní alternativu a nabízelo by celkově vyšší úspory hmotnosti.
Podívejme se na obdobnou a mnohem rozsáhlejší studii návrhu surové karoserie (body in white, BIW) u automobilů třídy C. V tomto případě jsou nejdůležitějšími hledisky torzní tuhost a mnoho případů havárií z různých směrů.
Obrázek 11 zobrazuje výsledný návrh. V tomto případě se ukazuje, že jediným rozumným materiálem by byl materiál na bázi uhlíkových vláken. Úspory hmotnosti by byly značné – více než 150 kg v případě BIW o hmotnosti kolem 300 kg. Používání termoplastových kompozitů by umožnilo řešení lehkých spojovaných konstrukcí, které vyžadují svařování. Nicméně s ohledem na současné ceny uhlíkových vláken je dosažení přijatelných nákladů na lehkou konstrukci při velkém objemu výroby automobilů stále náročným úkolem. Termoplastové kompozity by byly pravděpodobně postupně zaváděny u jednotlivých dílů na základě atraktivity možností integrace nebo výborných hodnot absorpce energie u prvků pohlcujících kinetickou energii nárazu.
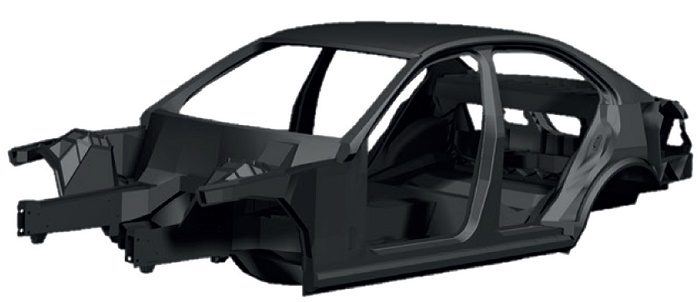
Obrázek 11:surová karosérie z uhlíkových vláken
Všechny tyto studie využívají analýzu CAE prováděnou na základě technických dat materiálu a validovaných metod simulace.
Závěr
Řešení s použitím termoplastových kompozitů nabízí proveditelné možnosti, jak dosáhnout žádoucích lehkých konstrukcí v hromadné automobilové výrobě.
Faktory úspěchu při implementování této strategie zahrnují: nevyměňovat jednoduché plechové díly „jeden za druhý“; namísto toho vybrat složené komponenty a využít potenciál integrace dílu, který nabízí plastové díly se zálisky, navrhovat komponenty tak, aby byl podíl zálisků co největší a náklady co nejnižší, pokud je to možné, používat formy materiálů na bázi UD tak, aby byly mechanické vlastnosti co nejlepší a náklady na kg uspořené hmotnosti co nejnižší.
Pokud se chcete dozvědět více informací: www.sabic-europe.com
Pokud není uvedeno jinak, SABIC a značky označené (TM) představují obchodní značky společnosti SABIC nebo jejich dceřiných společností nebo přičleněných organizací. Veškeré značky, produkty nebo služby jiných společností uváděných v tomto článku představují obchodní značky, značky služby anebo obchodní názvy jejich příslušných držitelů.
WARDEN SCHIJVE
Vedoucí výzkumného týmu kompozitů GINO FRANCATO
Manažer pro evropský marketing – uvádění kompozitů na trh SABIC
www.sabic-europe.com
Mohlo by se Vám líbit
Výroba kyčelních endoprotéz s pomocí měřicích strojů Hexagon a softwaru PC-DMIS
- Strojírenství
-
17. července 2025
Francouzská společnost Dedienne Santé se zaměřuje na výrobu implantabilních zdravotnických výrobků, zejména totálních náhrad kyčelních kloubů. Specializují se na tzv. náhrady s „dvojitou mobilitou“, kdy […]
DC napájecí konektory od firmy Amphenol GEC
- Elektro
-
16. července 2025
Řešení PowerLok™ navržená pro aplikace EV. Nabídka firmy TME byla rozšířena o zásuvky PowerLok™ od firmy Amphenol GEC. Jedná se o novou nabídku od renomovaného […]
Bezkontaktní monitorování frekvence a výkonu vysokofrekvenčního ultrazvuku
- Elektro
-
15. července 2025
Inovativní řešení APM od společnosti Ecoclean zajišťuje účinnost čištění megazvukem Monitorování frekvence a výkonu je důležitým nástrojem pro zajištění kvality ultrazvukového čištění v rozsahu 250 […]