02. dubna 2019 16:28
ASTRA MOTOR – principy Industry 4.0 nám zdvojnásobily obrat při stávajícím počtu zaměstnanců
Českou rodinnou firmu ASTRA MOTOR spol. s r. o. jsme měli možnost navštívit v brněnských Horních Heršpicích. Společnost, která se zabývá výrobou speciálních monolitických nástrojů, je jednou z mála svého typu v České republice, která má velké ambice v oblasti zavádění Industry 4.0 – a je v tom velmi úspěšná.
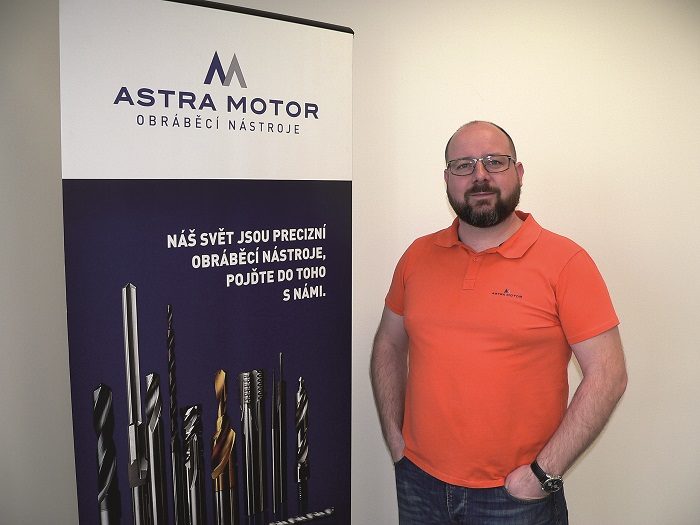
Pan Ing. Jan Keprda, jednatel společnosti ASTRA MOTOR spol. s r. o.
A to není zdaleka jediná věc, která nás při návštěvě v této firmě překvapila. Zaujala nás také její filozofie „výroba nástrojů jako komplexní služba“, která je promítnuta do celé společnosti, její koncept vzdělávání zaměstnanců na všech úrovních, moderní výrobní hala s novými výrobními stroji, procesy a postupy. Zaujal nás ambiciózní projekt kompletní digitalizace společnosti, ale i takové „detaily“ jako je management hospodaření s řeznými oleji na obráběcích strojích.
ASTRA MOTOR začala, pod vedením pana Karla a Jana Keprdových, s ostřením obráběcích nástrojů už v roce 2001. Záhy se pustili i do vývoje a výroby. Jejich hlavní myšlenkou bylo, aby firma prodávala nástroje jako komplexní službu, což zůstalo dodnes. Od té doby se ovšem společnost posunula o velký kus vpřed. O tom všem a mnohem více si můžete přečíst v rozhovoru.
Pane Keprdo, čím se Vaše společnost zabývá?
Zabýváme se speciálními nástroji. Měsíčně jich z naší firmy odejde asi 9 000 ks. Vyrábíme a servisujeme většinu typů monolitických tvrdokovových rotačních nástrojů. Jsou to vrtáky, frézy, výstružníky, částečně i závitovací nástroje, záhlubníky a dlouhé vrtáky. Jako jediní v republice, a jedni z mála v Evropě, máme stroj na výrobu tvrdokovových dlouhých spirálových vrtáků, na kterém jsme schopni vyrobit nástroj v délce až 100násobku jeho průměru (100D). Naše nástroje nachází uplatnění v automotive, energetice, letectví a podobně.
Dodáváte i do zahraničí?
Ano, mimo tradičních zákazníků v EU například i do automotive v Mexiku.
Ve společnosti se řídíte heslem „výroba nástrojů jako komplexní služba“, co to přesně znamená?
Snažíme se nástroje nedodávat jako produkt, ale jako službu – jako řešení. Nositelem služby je samozřejmě produkt, ale okolo něj je hodně věcí, které se musí vyřešit.

Pan Ing. Jan Keprda nám vysvětluje, jak fungují jejich komplexní služby
Jak to funguje v praxi?
Zákazníci řeší různé problémy – jeden chce zrychlit proces, dalšího trápí krátká životnost nástrojů nebo i třeba málo místa v zakladači atd. My potřebujeme vstupní informace, co vyrábí, jak rychle, jak přesně, na jakém stroji a další vstupní podmínky. Na základě toho navrhneme nejlepší individuální řešení. Nehledáme v katalogu hotových možností, ale vyvíjíme mu řešení na míru. Dodáme optimalizované nástroje, řezné podmínky, pomůžeme s odladěním procesu, předáme. Cíle je dosaženo, zákazník se o to nemusí starat, což mu ušetří další čas i peníze. Funguje to velmi dobře.
Řešíte se zákazníkem jednotlivé obráběcí operace nebo i složité komplexní projekty?
Momentálně pracujeme na velkém projektu pro jednoho zákazníka, kde vstupními informacemi bylo pouze: tady máme stroj se základními parametry, tady výrobek, na kterém je několik set obrobených ploch, děr atd. Naše představa je taková, že cycle time bude asi 45 minut. Prosím pošlete nám nabídku, výkresy, technologii, prostě kompletní řešení. A tohle jsou typy zakázek, které obvykle dělají jenom velcí dodavatelé nástrojů. Přestože jsme menší firma, tak jsme schopni tyto požadavky splnit také. Nejen proto, že se od začátku na výrobu nástrojů díváme jako na komplexní službu, ale i proto, že máme kolem sebe další firmy, se kterými spolupracuje. My vyrábíme monolity, někteří dělají destičkové nástroje, další zase soustružnické nástroje atd., společně jsme ale schopni vytvořit něco jako konsorcium dodavatelů nástrojů. Ve strojírenství tato spolupráce není úplně běžnou praxí, na rozdíl od stavebnictví, ve kterém je to úplně normální… Myslím si, že je to velká škoda.

Pan Ing. Keprda nám vysvětluje jednotlivé aspekty komplexní služby zákazníkovi
Zmínil jste se, že takto komplexní projekty můžete dělat především díky spolupráci s ostatními firmami a proto, že se na výrobu nástrojů díváte jako na službu… Máte ještě nějaké další zásady nebo postupy, abyste byli schopni tyto projekty zrealizovat?
Máme vlastní vývoj, konstrukci, technologii a výrobu a ve spolupráci s různými zákazníky a výzkumnými institucemi naše nástroje intenzivně testujeme. Díky tomu máme vlastní geometrie, takže víme co, kde, na co funguje. A když přijde zákazník s nějakým problémem, je většinou hodně podobný s jiným už někde vyřešeným, takže stačí určitá personifikace. Pokud je to naprosto ojedinělý požadavek či problém, o to lépe – máme inspiraci pro další výzkum a posouvá nás to vpřed. Dále si velmi striktně si zakládáme na tom, že se všechny nástroje kompletně vyrábí u nás. Celý proces, mimo povlakování, si díky tomu řídíme sami. Chceme mít stoprocentní kvalitu a proces pevně v rukou – abychom na něj viděli. A díky tomu jsme taky schopni jakýkoliv případný problém podchytit. Jedinou výjimkou je povlakování. Jedná se o naprosto odlišný obor, který se rozvíjí tak rychle, že všechny firmy podobné velikosti jako my, které si koupily svoje vlastní povlakovací centra, měly po dvou, třech letech zastaralé produkty. Dnes spolupracujeme s pěti dodavateli povlakování a většinou každý rok přichází s nějakou novinkou, která obor povlakování posouvá zase o něco dál. Navíc můžeme vždy použít ideální povlak pro danou aplikaci u zákazníka, a nejen ten který bychom my sami dělali, k čemuž by to svádělo.
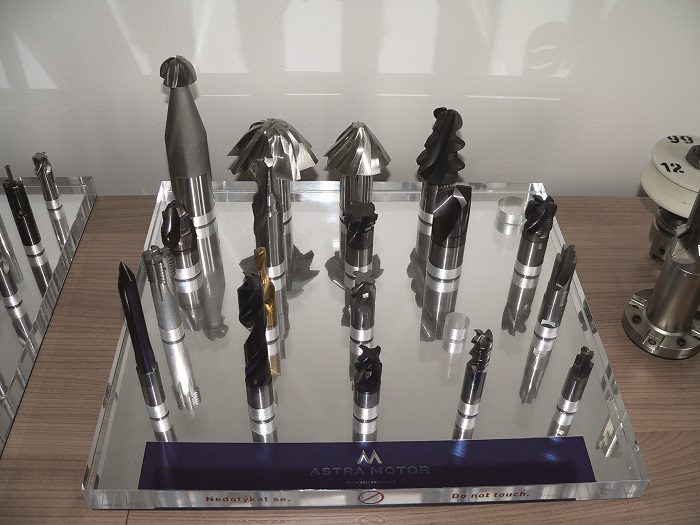
Příklady nástrojů, které společnost ASTRA MOTOR vyrábí
Říkal jste, že díky Vašim komplexním službám dodáváte zákazníkům řešení efektivnějšího obrábění. Kde ještě vidíte u zákazníků možnost zlepšení efektivity výroby?
Já si netroufnu říct, že v nástrojárnách je problém tady a v automobilkách tady… V naší firmě například děláme zakázkovou výrobu, což je z hlediska efektivity práce to nejhorší, co může být. Stále děláme něco nového, ale i přesto můžeme najít činnosti a procesy, které se opakují. Ty můžeme standardizovat a zmenšit počet variant. Někdy nám to pomůže, ale někdy zase zjistíme, že nám to v podstatě nic moc neubírá… Nedávno jsem se byl podívat v automobilce Porsche v Zuffenhausenu, kde se vyrábí typ 911. Na první pohled to je standardní pásová výroba. Ale zákazníci těchto aut mají rádi individualizaci, ale ne takovou, jakou známe z normálních aut „vyberte si z těchto možností“ ale opravdovou, chtějí věci, které nikdo jiný na světě nemá. A najednou je z toho v podstatě hromadná kusová výroba! Je přesně vidět, kde se dají využít moderní stroje, procesy, technologie a kde jsou pořád potřeba lidé. Protože je to nejefektivnější. Dle mého názoru je problém, že spousta firem přemýšlí, jak úplně všechno zefektivnit a zautomatizovat. Ovšem i dle Gaussovy křivky máte nějakou část procesů, kterou má smysl řešit automatizací, pak jsou okrajové věci, na které jsou potřeba šikovní lidé.
Bavíme se tady o výrobních procesech, efektivitě a automatizaci výroby. To jsou všechno důvody, které přivedly vaši firmu do Industry Clusteru 4.0. Můžete nám tuto organizaci představit?
Já tomu říkám zájmové sdružení filatelistů (smích). Do klastru přicházíte s určitými zkušenostmi a setkáváte se s ostatními lidmi, kteří mají zase jiné zkušenosti. Takže když například řešíte nějaký problém a jiný člověk v klastru má podobný problém již vyřešený, můžete aplikovat jeho řešení. Samozřejmě, klastr se také zabývá osvětou, poradenstvím, organizováním sympozií, jezdíme po světě a díváme se, jak to dělají jinde apod. My jsme se do Clusteru 4.0 dostali díky úžasné Regionální hospodářské komoře Brno, jejímiž jsme členy. Pro nás, členy IC4.0, je to skvělé v tom, že se jednou za čas scházíme s tím silným jádrem klastru, lidmi, které to baví a jsou pro to zapálení. Ze začátku vás to spíš musí bavit, než aby v tom člověk viděl okamžitý ekonomický přínos pro firmu. Velký přínos tam samozřejmě je, ale ze začátku je to o tom, že by člověk měl přemýšlet co vlastně může pro svoji společnost v rámci myšlenky Industry 4.0 udělat. Osobně vidím největší problém v tom, že hodně lidí zavádí Industry 4.0, protože je to „moderní“ a dělají něco, co pro firmu nemá žádný efekt. V IC4.0 si můžete popovídat s dalšími lidmi z různých společností a jste schopni si najít svoji vlastní realitu, řešení, které se dá implementovat i u nás. Tyto aktivity pro nás představují obrovský přínos. Za poslední tři roky jsme při zachování stejného počtu zaměstnanců zdvojnásobili obrat. A není to o ničem jiném než o efektivním využití zdrojů – výrobních, lidských i informačních.
Při stejném počtu zaměstnanců jste zdvojnásobili obrat díky Industry 4.0? To je úžasné…
Ano, dnes máme dvě firmy: ASTRA MOTOR, která je výrobní a ASTRA MOTOR INTERNATIONAL, zaměřenou na zahraniční obchod. Obrat máme okolo 70 milionů korun a letos bychom mohli překročit 80 milionů. Náš růst se poslední 3 roky pohybuje mezi 15–20 % za rok. Rosteme rychleji, než rostou naše teoretické kapacity. To vše souvisí se zvyšováním efektivity a eliminací ztrátových časů, které jsou často schované v místech, kde by to málokdo čekal. Jsou to věci, u kterých si člověk řekne, že zkrátit nejdou. A najednou zjistíte, že ušetříte 10 % času, a to je balík peněz, který zase můžete investovat do rozvoje firmy…
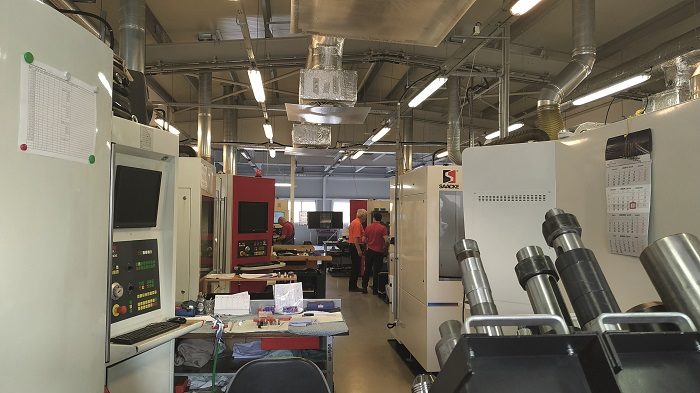
Pohled do nové výrobní haly společnosti ASTRA MOTOR
Takže zavádíte do vaší výroby i metody jako například Kaizen…?
Kaizen je filozofie – jediná jistota je změna. Bez toho se nikam nepohnete. Obávám se ale, že pomalu končí doba, kdy tyto metody stačily. Atomový Jack Welch zachránil General Electric před pádem do propadliště dějin díky zavedení „moderních metod řízení změn“ Kaizen, Ishikawa, atd. Ale tyto metody vznikly po 2. světové válce. To je více než 80 let! A nejde o to, že by to dnes nefungovalo, ale doba se mění a to velice rychle. Dnes už to nestačí. Potřebujete analyzovat takové množství dat, že to bez nějakého I4.0 nástroje prostě nemáte šanci pojmout.
Pomáháte v rámci vašich komplexních služeb zákazníkům nějakým způsobem i s Industry 4.0?
Ne, takový produkt nemáme. Do vrtáku nedostanete žádná čidla, která by něco řešila. My zákazníkům pořád dodáváme „jen“ vrták. Pár firem něco podobného zkoušelo s destičkami, ale v podstatě bez nějakého rozumného efektu. Takže s Industry 4.0 u zákazníka nehneme, to musí on sám. Myslím, že základní problém je, že si málokdo pod pojmem Industry 4.0 představí, co to opravdu znamená. Lidé si pod tímto pojmem obvykle představí něco jednoduchého. Máme robota, tak máme I4.0. Už ale neřeší, že se k tomu váže další hromada procesů, která je s tím spojená a je ji potřeba také řešit. Po těchto robotech, přichází softwaroví roboti, kteří budou schopni analyzovat velké množství dat (big data), na které už naše mozky nestačí. Hledají se příčiny nestandardního chování procesu, neshod, výpadků atd. a to napříč celou firmou. Propojují se zdánlivě nesourodé výstupy, hledají se průniky a nachází řešení. A na toto je brainstorming s Ishikawovou kostí už krátký. Jedna zajímavá příhoda: Nejmenovaná firma připojila komplet celou firmu na sběr dat. Ale opravdu vše, od příchodů lidí do firmy, teplotní a výkonová čidla, až po poslední výrobní proces. Vše, co mělo konektivitu a co šlo sledovat „napíchnuli“. Veškerá data sypali do cloudu a po nějaké době na tyto data nasadili softwarového robota. Základní požadavek byl najít příčiny kolísání produktivity. Mimo relativně standardních zjištění tam vyskočil i jeden velice zajímavý. Při ranní směně se cyklicky snižovala efektivita výroby. Z analýzy jim vyšlo, že pokud změní začátek pracovní doby z 6:00 na 7:15, zvýší se efektivita na ranní směně o 12 %. Zkusili to na nějakém vzorku výroby a opravdu to fungovalo. Ale dodnes neví proč. A tohle jsou věci, které člověk už není schopen pojmout. Takové informace mu dodá až to zařízení. A o tom je Industry 4.0.
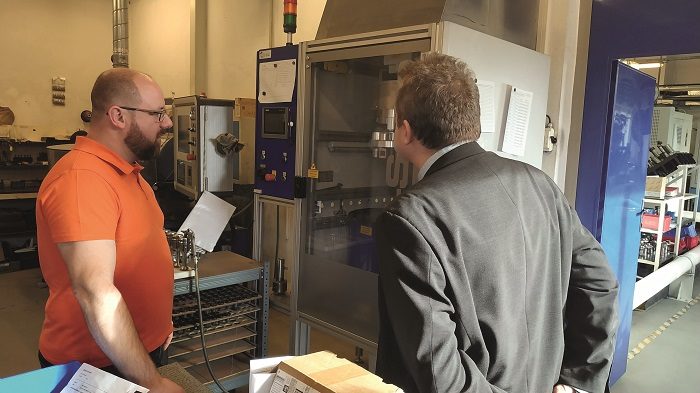
Naše redakce při prohlídce výrobní části firmy
Co Vám při zavádění Industry 4.0 ve vaší společnosti nejvíce pomohlo?
Pomohlo nám, že jsme se podívali dovnitř firmy, ale i ven. Také nám opravdu moc pomohly dobré kontakty z Hospodářské komory a IC4. 0. Ne kvůli tomu, že bychom získali nějaký kšeft. Ale proto, že jsme se dostali k zajímavým lidem, kteří nám otevřeli oči, co by se v naší firmě dalo dělat. Je to opravdu jen o tom potkávat se s lidmi… poslouchat je a vnímat to co říkají… Velmi nám pomohlo i zavedení systému vzdělávání lidí. Zjistil jsem, že vzdělávání zaměstnanců není o tom vzdělávat je od funkce technologa a výš, protože pak si technolog s pracovníky na dílně vůbec nerozumí. Naopak naši zaměstnanci se vzdělávají od úrovně pracovníků z dílny, kteří fyzicky pracují na strojích, až po nejvyšší management. Všichni absolvují kurzy tvrdých i měkkých dovedností, jako jsou komunikační a prezentační dovednosti, moderní metody řízení. Díky tomu se jim zlepšily různé schopnosti, ale také se jim zvedla ochota a sebedůvěra. Dnes za mnou chodí zaměstnanci přímo z dílny a sami navrhují, jak výrobu ještě více zefektivnit. A čím více jsou tito lidé, kteří fyzicky pracují u strojů, vzdělanější, tím lépe se nám dělají i různé změny. Například když někdo přijde do dílny s novou myšlenkou efektivnějšího řešení výroby, zeptáme se nejprve na jejich názor a společně se pak snažíme vymyslet, jak toto řešení zavést do praxe. Spousta firem má problém, že při pořízení nového stroje s robotem, se lidé v dílnách začnou bát o práci. U nás to tak vůbec nefunguje. Naši zaměstnanci dobře ví, že když pořídíme nový stroj s robotem, jsou tam pořád potřeba, aby stroj řídili, a že se zvedne efektivita výroby, která jim umožní obsluhovat dva, tři nebo čtyři stroje najednou. Dnes máme ve společnosti zavedenou i „čtyřstrojovku“ a automatické provozy. A pracovníci v dílně chodí vysmátí, protože kolem strojů nemusí běhat tolik, jako v minulosti. Na konci minulého roku jsme dělali mezi všemi lidmi dotazník spokojenosti, ve kterém jsme, ačkoli nás od toho mnoho lidí odrazovalo, použili metodu otevřených otázek. I přes počáteční obavy, jsme při vyhodnocení zjistili, že většina odpovědí dává smysl. Takže, abych to shrnul, díky zavedení systému vzdělávání, můžeme s lidmi ve společnosti pracovat úplně jinak a rozvoj firmy se také dělá mnohem lépe.

Pracovní pohoda v ASTRA MOTOR
Co pro Vás bylo největší inspirací v oblasti 4.0?
Asi největší inspiraci v oblasti 4.0 jsem zažil v pekárně! Zcela mimo náš obor. Průmyslová pekařina je něco úžasného, řekl bych, úrovní tak Industry 8.0 (smích). Byl jsem se podívat v jedné moderní pekárně s kapacitou více jak 1,2 mil. rohlíků denně. Celou pekárnu obsluhuje pár lidí a vše je automatizované. Lidská ruka se pečiva nedotkne. Od vstupu surovin po expedici. Dokonce když přijede auto pro rohlíky, které je rozváží do obchodů, naloží se mu do auta vše připravené tak, jak je řidič postupně bude z auta vytahovat. To je prostě úžasné.
Jaké máte plány při zavádění Industry 4.0 ve Vaší firmě do budoucna?
Momentálně pracujeme na velkém projektu kompletní digitalizace firmy. Jednoduše žádné papírování. Díky tomu budeme vědět o každém nástroji úplně všechno, včetně nástrojů, které servisujeme. Budeme schopni predikovat stav nástroje a zjistíme, jaký servis máme dělat a zda to má vůbec smysl. To celé budeme směřovat k tomu, aby ze všech dat vyšly informace, které dnes ještě nevíme. Profit bude i pro zákazníka, protože bude mít včas informace, díky kterým bude schopen například lépe plánovat nákup nových nástrojů či předvídat budoucí náklady atd. Druhá část projektu je stabilizace výroby. My vyrábíme na jednotky mikronů. V těchto přesnostech je jakákoliv destabilizace ve výrobě okamžitě vidět. Všude například udržujeme stabilní teplotu 24 stupňů, jak ve výrobě, tak v měřící místnosti. Ve všech strojích máme olej čištěný na 99,99 %, částice větší jak 1 mikron se odfiltrují. Vytváříme tedy krystalicky čistý olej, který chladíme také na 24 stupňů, plus mínus půl stupně. Avšak i přes to existují výkyvy, u kterých nevíme, proč se dějí. Některé typy nástrojů můžeme dělat jen v určitou denní dobu. Například mezi druhou a čtvrtou hodinou odpoledne se nepravidelně objevuje výkyv rozměrové stability, takže v tomto čase ty nejpřesnější nástroje nevyrábíme. Za 10 let, co jsme v nových prostorech, jsme stále nepřišli na to, proč se tyto výkyvy dějí. Nyní máme k dispozici dvě cesty, jak tento problém řešit. Cesta standardní, tzn. ještě více ten proces zpřesnit, ještě zlepšit, nainvestovat do toho… zdvojit, ztrojit, zečtyřnásobit jistotu a pak výkyvy třeba přestanou. Anebo cesta druhá, cesta I4.0. Vzít informace z čidel strojů, sbírat data například rok do cloudu, a přes robotickou analýzu zjistit, proč se výkyvy dějí. Pak zjistíme, že například ve stejnou chvíli se potká několik faktorů dohromady a vznikne daný problém…

Sběrná nádrž řezného oleje společná všem obráběcím strojům
Průmysl 4.0 je pro nás reálnou cestou, jak ještě více zefektivnit výrobní procesy, kvalitu produkce a zdokonalit tak naši komplexní službu, kterou přinášíme zákazníkovi!
Pane Keprdo, děkujeme Vám za rozhovor a přejeme Vám mnoho úspěchů do dalších let!
Nikol Laifrová, Jiří Klusáček, redakce
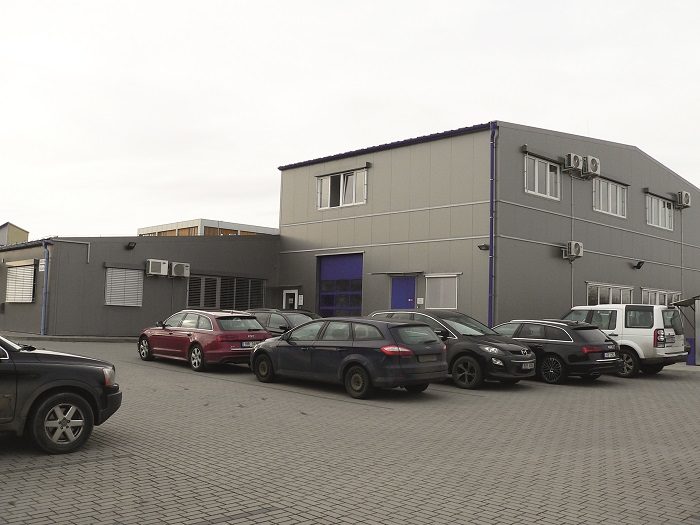
Sídlo společnosti ASTRA MOTOR
Mohlo by se Vám líbit
Zařízení Ixxat Mobilizer přinášejí zásadní změnu při testování i výrobě automobilů
- Automotive
-
28. června 2025
Společnost HMS Networks představila pod svou produktovou značkou Ixxat nejmodernější komunikační brány řady Mobilizer pro automobilový průmysl. Komunikační brány Mobilizer jsou navrženy tak, aby splňovaly […]
Pracovní rizika pod kontrolou: co ovlivňuje zdraví zaměstnanců a jak tomu předcházet. Od roku 2025 platí nově povinnost bezpečnostních pracovních přestávek či lepšího osvětlení.
- Práce
-
26. června 2025
Bezpečné pracovní prostředí není pouze o splnění povinností vůči legislativě. Dlouhodobé vystavení škodlivým faktorům může mít negativní dopady na zdraví zaměstnanců i na jejich výkonnost, […]
Přihlaste se do konce června a zajistěte si účast na veletrhu za nejvýhodnějších podmínek
- Elektro
-
24. června 2025
Od 17. do 19. 3. 2026 se na brněnském výstavišti koná další ročník veletrhu AMPER. Nově se na AMPER můžete přihlásit i elektronicky. Pokud to […]