14. října 2018 14:39
Bez měření to nejde
Uživatelé obráběcích strojů jsou často konfrontováni s protichůdnými požadavky: vyrábět co nejlevněji, vyrábět co nejrychleji, vyrábět co nejpřesněji.
Tři kritéria uvedená v podtitulu se na první pohled vzájemně vylučují. Při bližším rozboru můžeme zjistit, že jejich splnění je možné za určitých podmínek. Z obráběcího stroje je třeba dostat v nejkratším možném čase 100% dílců, jejichž rozměry budou odpovídat tolerancím uvedeným na výkrese. Mnoho obráběcích strojů je vybaveno měřicími sondami pro ustavení a kontrolu obrobku nebo pro seřízení a kontrolu nástroje. Technolog, CNC programátor dokáže pomocí těchto nástrojů radikálně omezit vliv ručního ustavování, vliv nepřesného upnutí obrobku nebo třeba vliv únavy pracovníka obsluhujícího stroj. Výše uvedená kritéria však zřetelně naznačují, že jejich splnění není tak jednoduché.
Společnost Renishaw, na základě svých vlastních zkušeností s výrobou a zlepšováním výrobního procesu pracuje s konceptem nazvaným Pyramida produktivního procesu.
Tento koncept názorně vysvětluje, jak mohou uživatelé obráběcích strojů díky měřicím systémům zlepšit výrobní proces. Celý proces výroby můžeme rozdělit do čtyř fází, a to přípravy výroby, nastavení parametrů procesu, zpětnou vazbu a celou pyramidu uzavírá kontrola hotových dílů.
- PŘÍPRAVA VÝROBY je hlavním preventivním opatřením
Opatření provedená v základní vrstvě pyramidy jsou zaměřena na stabilitu prostředí, ve kterém bude obrábění probíhat.
Tato preventivní opatření musí zabránit tomu, aby se v průběhu obrábění objevily jakékoliv neočekávané vlivy, které by mohly způsobovat nahodilé chyby. Základním preventivním opatřením je optimalizace stavu stroje. Je to základní předpoklad pro přípravu výroby, bez kterého nelze realizovat jakoukoli výrobu.
Na nepřesném stroji nelze přesně vyrábět. Na základě vyhodnocení zjištěných parametrů stroje lze po re-kalibraci nebo softwarové kompenzaci geometrické přesnosti stroje, seřízení pohonů, popřípadě mechanické opravě dosáhnout takových vlastností stroje, které umožňují obrábění v rámci požadovaných hodnot.
Nejdůležitější je příprava a seřízení stroje. Geometrickou přesnost tříosého obráběcího stroje ovlivňuje až 21 geometrických chyb. Jedná se o chyby lineárního polohování, chyby přímočarosti pohybu stroje v jednotlivých osách, chyby naklopení a natočení v osách a chyby kolmosti jednotlviých os vůči sobě. V případě pětiosého stroje se počet těchto potenciálních zdrojů nepřesností zvyšuje až na hodnotu 36.
Kromě chyb geometrie se na celkové přesnosti stroje významně projevují dynamické nepřesnosti, kterými jsou vůle v posuvech, seřízení servopohonů, seřízení počátků odměřovacích pravítek v jednotlivých osách stroj a celá řada dalších faktorů.
Všechny výše uvedené chyby dosahují hodnot v řádu mikrometrů. Každá z nich však má nepříznivý vliv a celkovou přesnost polohování stroje a na tvarovou a rozměrovou přesnost obrobků. Výsledkem je produkce rozměrově nepřesných dílců, nestabilita výrobního procesu, tvarové odchylky obráběných prvků na dílci nebo nekvalitní povrch obrobku. Tyto chyby lze s použitím vhodného diagnostického nástroje zjistit. Některé z nich je nutno eliminovat mechanickým seřízením nebo opravou, avšak mnoho z nich lze kompenzovat vhodným nastavením parametrů v řídícím systému stroje.
Jedním z takových diagnostických nástrojů je měřicí system Ballbar QC20 (obr. 1). Použití přístroje je rychlé a jednoduché. Naměřená data se analyzují v souladu s platnými normami, například ISO230-4. Unikátní algoritmy z naměřených hodnot vyhodnotí 15 geometrických chyb, zobrazí jejich průběh a hodnoty. Výsledky jsou doplněny textovým výstupem v českém jazyce, který objasní příčiny chyb a jejich projevy na hotovém obrobku. Díky Ballbaru můžete pravidelně kontrolovat technický stav Vašeho stroje a plánovat případné opravy. V případě kolize pak můžete rychle rozhodnout, zda je možné pokračovat v produkci nebo volat servis.
- NASTAVENÍ PROCESU je opatřením před začátkem obrábění
Nastavením procesu se rozumí seřízení soustavy stroj–obrobek–nástroj před započetím obrábění. Je třeba správně identifikovat polohu a velikost obráběného dílce, díl ve stroji, zjistit přídavky na obrábění a udělat aktuální korekce nástrojů. Málokterá strojírenská firma dlouhodobě vyrábí velké série omezeného množství výrobků pro které je ekonomicky únosné vybavit stroj drahými specializovanými upínači přesně definujícími polohu obrobku ve stroji.
Mnohem častější situací je produkce množství různých výrobků vyžadujících komplexní obrábění v malých sériích a ve velmi krátkém čase. Nastavení procesu lze rozdělit do tří oblastí:
V případě Seřízení stroje se jedná o vyrovnání upínacích přípravků, rotačních os a indexovacích zařízení, které budou použity k ustavení a upnutí obrobku, nastavení správné polohy referenčních bodů na upínačích a středu osy otáčení indexovacích zařízení.
V případě Ustavení obrobku se jedná o identifikaci dílce a výběr správného NC programu, ustavení polohy referenčního prvku na dílci a natočení pracovního souřadného system stroje, zjištění přídavku na obrábění a určení hloubky třísky pro hrubovací a dokončovací operace, správnou orientaci dílce na stole stroje tak, aby bylo možné při obrábění dosáhnout na požadované plochy.
V případě Seřízení nástroje se jedná o nastavení délky nástroje vzhledem k referenční ploše nebo referenčnímu nástroji, zavedení odpovídající nástrojové korekce a kontrolu, že takto nastavená délka je v mezích požadované tolerance, nastavení průměru rotujícího nástroje a zavedení odpovídající nástrojové korekce (obr. 2 – dynamické ustavení obráběcích nástrojů na stroji pomocí nástrojové sondy OTS).
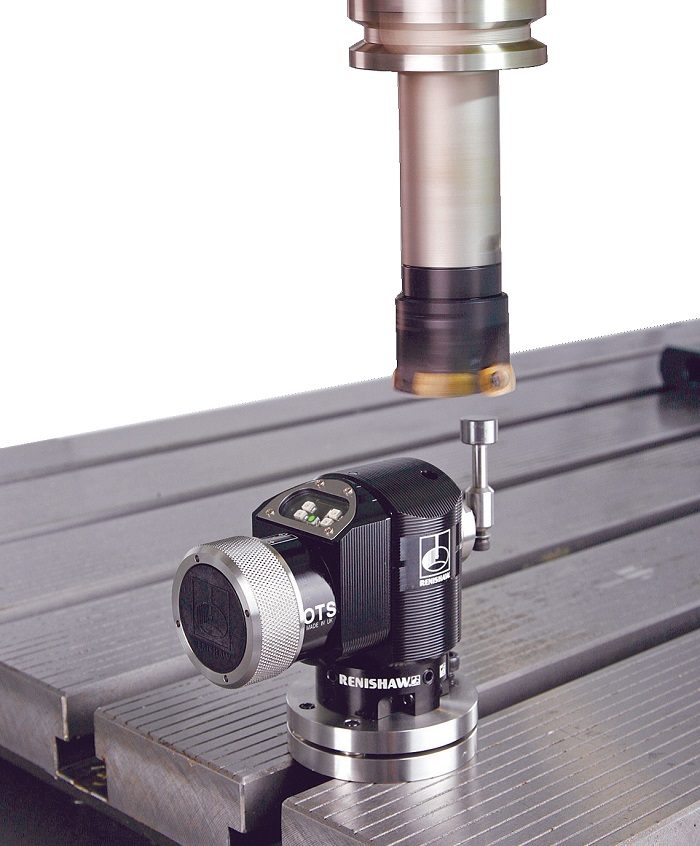
obr. 2
CNC obráběcí stroje nevyžadují perfektní vyrovnání obrobku. Řídící systémy obráběcího stroje umožňují podle aktuální polohy dílce upravovat posunutí a natočení pracovního souřadného systému stroje. Ustavení obrobku je klasický příklad využití měřicích sond. Zpravidla se jedná o identifikaci polohy rohu dílce nebo středu otvoru, které jsou využity jako nový počátek pracovního souřadného systému. Další změřený prvek, například bod na ploše nebo střed dalšího otvoru poslouží ke zjištění úhlu natočení obrobku. Vyrovnání pracovního souřadného systému stroje se souřadným systémem obrobku je pak otázkou jednoduché rutiny integrované v řídícím systému stroje spuštěné jediným povelem z technologického programu.
V případech obrábění odlitků nebo výkovků, kde kolísá rozměrové provedení hrubého polotovaru je důležitým parametrem zjištění velikosti přídavku na opracování. Příprava technologického programu pro maximální velikost přídavku znamená časté obrábění naprázdno, kdy se nástroj pohybuje někdy i v několika cyklech nad povrchem polotovaru. Díky měřicí sondě lze s použitím velmi jednoduché logiky větvení programu dosáhnout produktivního obrábění bez ohledu na velikost dodaného polotovaru.
Dalším aspektem nastavení parametrů před obráběním je zjištění délky a průměru nástroje a jejich korekce v případě opotřebení. Seřízení nástrojů pomocí sond však není omezeno jen na délku a průměr. Nástrojová sonda umožňuje kontrolovat také tvar břitu nástroje a jeho celistvost. Ve všech výše vedených aplikacích má nasazení měřicích sond jeden společný významný efekt. Eliminace omylů a chyb způsobených lidským faktorem. Opakovaně přesné měření a automatická korekce naměřených údajů bez ohledu na únavu nebo momentální indispozici operátora stroje jsou faktory, které významně ovlivňují rozhodování o investici do měřicích sond.
- AKTIVNÍ ZPĚTNÁ VAZBA je opatřením v průběhu obrábění
Opatření v této vrstvě Pyramidy zahrnují činnosti a akce prováděné v průběhu obrábění. Tato opatření automaticky vytvářejí odezvu na stav materiálu, na aktuální odchylky od očekávaných rozměrů nebo na jiné neočekávané stavy procesu. Díky těmto odezvám lze proces ovlivňovat a řídit směrem k očekávanému výsledku.
Měření obrobku během cyklu obrábění umožňuje na základě zjištěných hodnot reagovat na odchylky způsobené například deformací dílce, vychýlením nástroje nebo vlivem teplotních deformací (obr. 3 – měření obrobku pomocí obrobkové sondy RMP40). Na základě zjištěných hodnot lze automaticky upravit aktuální hodnoty natočení souřadného systému, aktualizovat parametry obrábění, změnit korekční hodnoty v tabulkách nástrojů a větvit chod programu pomocí logických podmínek tak, aby výsledkem byl bezvadný výrobek.
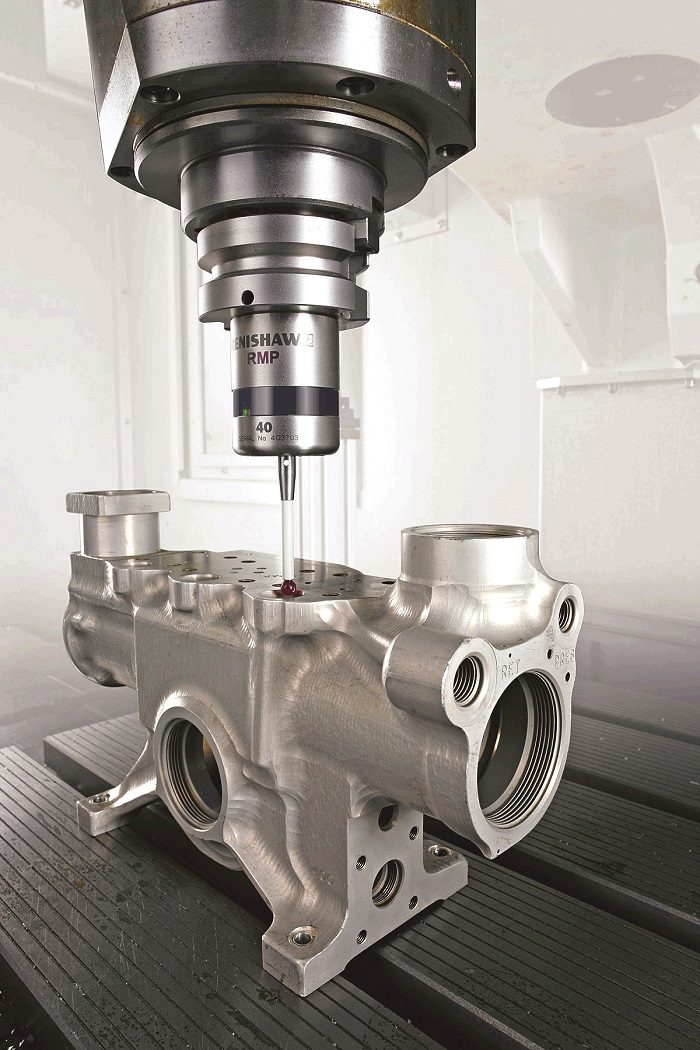
obr. 3
Detekce poškození a opotřebení nástrojů umožňuje kontrolu přítomnosti a polohy nástroje, kontrolu celistvosti a opotřebení břitů nástroje nebo kontrolu velikosti opotřebení nástroje a jeho automatickou korekci v tabulce nástrojů, popřípadě automatická sesterského nástroje nebo dokonce zastavení výrobního cyklu a volání operátora stroje. Aktivní kontrola procesu obrábění zahrnuje více než pouhou zpětnou vazbu a korekci parametrů v řídícím system na základě porovnání očekávané a zjištěné hodnoty. Aktivní kontrola procesu zahrnuje také nastavení mezí nebo limitů se kterými jsou naměřené hodnoty porovnávány. Na základě takto zjištěných výsledků přistupuje CNC obráběcí stroj automaticky k opravným procesům, které by měly vést ke zhotovení korektně vyrobeného dílce. Příkladem pro takovou aktivní kontrolu procesu může být měření průměru při soustružení v sériové výrobě. Skoková změna zjištěného rozměru, ke které může dojít z celé řady různých důvodů, by při okamžité korekci v jinak stabilním procesu znamenala rozkolísání celého procesu. Vhodně stanovené mezní hodnoty pro aplikaci korekčních parametrů pomáhají udržovat proces pod kontrolou. Zastavení produkce a volání operátora stroje je až krajním opatřením, které samozřejmě má svoje opodstatnění v určitých situacích.
- KONTROLA HOTOVÉHO VÝROBKU po dokončení obrábění
Vrchol Pyramidy představuje proměření vyrobeného dílu a získání výstupních informací z měření. Tyto údaje mohou být využity ke zdokumentování ukončeného procesu nebo k modifikaci procesu následujícího.
V praxi se nabízejí tři varianty kontroly geometrických rozměrů hotového dílce.
Varianta 1 – Měření hotového dílce přímo na stroji
Tento způsob měření umožňuje kontrolu důležitých prvků dílce přímo na stroji, před odepnutím a manipulací. Toto měření zřídka nahrazuje kontrolu rozměrů nezávislým měřidlem, ale poskytuje velmi dobrou představu o stabilitě produkce a v některých případech je dokonce jediným možným způsobem
jak dílec proměřit. Záznamy o měření získané přímo ze stroje a uložené v paměti stroje nebo odeslané prostřednictvím počítačové sítě na server mimo stroj dokumentují trendy procesu a kvalitu produkce. Historie údajů pak umožňuje monitorovat stav stroje a plánovat preventivní opravy a údržbu stroje.
Varianta 2 – Měření hotového dílce mimo stroje na souřadnicovém měřicím stroji
Tento způsob kontroly je nejobvyklejším v dnešní technické praxi. Přeměření prvního dílce ze série a kontrola namátkově nebo statisticky vybraných dílců ze série je běžnou praxí v mnoha strojírenských podnicích. Umožňuje komplexní přeměření všech důležitých rozměrů obrobku a jejich vyhodnocení
z hlediska geometrických rozměrů a tolerancí, ale i tolerance tvaru a polohy.
Varianta 3 – 100% kontrola produkce specializovaným kontrolním zařízením
Tento způsob kontroly byl velmi dlouho vyhrazen pro velkosériovou výrobu, zejména z důvodu cenové náročnosti specializovaných jednoúčelových měřidel. V posledních letech se 100% kontrola stává dostupnou i pro menší série dílců díky univerzálnímu porovnávacímu měřidlu Equator (obr. 4).
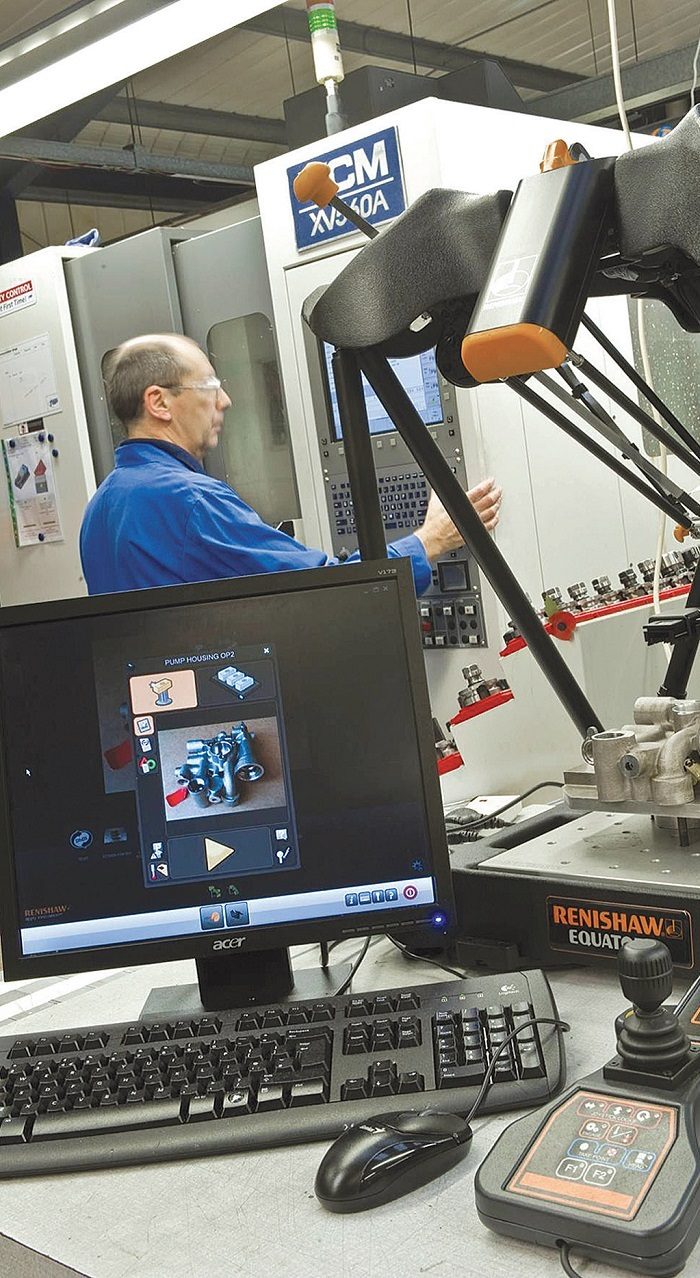
obr. 4
Mohlo by se Vám líbit
Výroba kyčelních endoprotéz s pomocí měřicích strojů Hexagon a softwaru PC-DMIS
- Strojírenství
-
17. července 2025
Francouzská společnost Dedienne Santé se zaměřuje na výrobu implantabilních zdravotnických výrobků, zejména totálních náhrad kyčelních kloubů. Specializují se na tzv. náhrady s „dvojitou mobilitou“, kdy […]
DC napájecí konektory od firmy Amphenol GEC
- Elektro
-
16. července 2025
Řešení PowerLok™ navržená pro aplikace EV. Nabídka firmy TME byla rozšířena o zásuvky PowerLok™ od firmy Amphenol GEC. Jedná se o novou nabídku od renomovaného […]
Bezkontaktní monitorování frekvence a výkonu vysokofrekvenčního ultrazvuku
- Elektro
-
15. července 2025
Inovativní řešení APM od společnosti Ecoclean zajišťuje účinnost čištění megazvukem Monitorování frekvence a výkonu je důležitým nástrojem pro zajištění kvality ultrazvukového čištění v rozsahu 250 […]