16. listopadu 2018 09:54
WITTMANN BATTENFELD AIRMOULD® ve WITTE Automotive: 300 barů stlačeného dusíku pod kontrolou
Výrobní závod německé skupiny WITTE Automotive, nově otevřený v Ostrově v severních Čechách v roce 2016, se specializuje na výrobu dveřních klik a zamykacích modulů ve spolupráci s dvacet kilometrů vzdáleným závodem v Nejdku. Jeho současná roční produkce se pohybuje okolo tří a půl milionu jednotek. Za tímto účelem funguje v Ostrově 14 vstřikovacích strojů WITTMANN BATTENFELD. Zhruba jeden milion klik je vyráběn jako dutý díl díky technologii vstřikování s podporou plynu WITTMANN BATTENFELD AIRMOULD®.
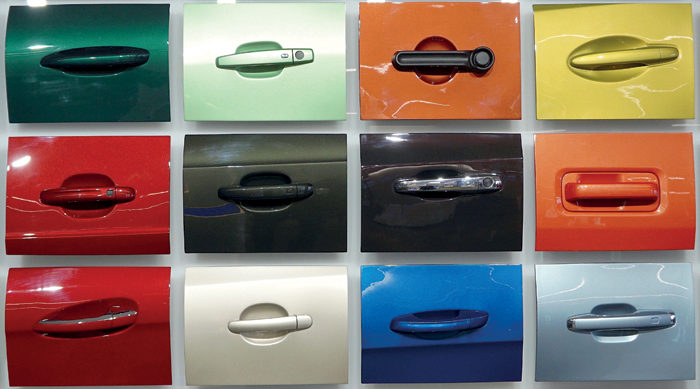
Obr. 1: Zaměření továrny WITTE Automotive, která byla otevřena v Ostrově v severních Čechách v roce 2016, je výroba dveřních klik do automobilů a k nim příslušejících zamykacích systémů

Obr. 2: Čtrnáct vstřikovacích strojů WITTMANN BATTENFELD ve WITTE Ostrov
s uzavírací silou od 1 800 do 5 500 kN ročně vyrábí okolo tří a půl milionu sestav dveřních klik pro automobily
Různorodost tvarů, barev a funkcí vnějších dveřních klik a zamykacích jednotek vyráběných ve WITTE Automotive v Ostrově, které musí také odpovídat přísným bezpečnostním regulacím pro crash‑testy, je impozantní. Přesto portfolio produktů skupiny WITTE Automotive obsahuje mnohem vice než pouze vnější dveřní kliky; zahrnuje také zamykací ramínka, systémy ovládání vnitřních dveří, zámky a klíče, přitahovače, systémy zajištění dveří, dveřní brzdy a motorizované dveřní pohony.
Zaměření na kvalitu povrchu
Jelikož majitelé aut dveřní kliky vidí i pociťují na dotek, jejich tvar a pohodlný úchop významně přispívá k celkovému dojmu kvality (obr. 1). K jejich produkci byl vystavěn nový závod v Ostrově u Karlových Varů v roce 2016 se čtrnácti vstřikovacími stroji WITTMANN BATTENFELD s uzavírací silou v rozmezí 1 800 až 5 500 kN, jakožto základním vybavením této továrny, v kombinaci s tří- a čtyřosými roboty WITTMANN a periferiemi pro následné automatické povrchové opracování vstřikovaných dveřních klik (obr. 2). Další rozšíření závodu na 20 výrobních buněk již probíhá. Kliky jsou vyráběny z materiálu PA6-GF30 (se třicetiprocentním vyztužením skleněnými vlákny), kryty ze směsi PC/ABS, za nimi umístěné strukturální komponenty z PP‑GF 30.
Požadavky na stále vysokou kvalitu vstřikovaných dílů zároveň s optimální energetickou efektivitou spolehlivě plní hybridní MacroPower E 500/2100, stroje vybavené plně elektrickou vstřikovací jednotkou a servo‑hydraulickou dvoudeskovou uzavírací jednotkou.
„Podle požadavku zákazníků vyrábíme tři různé druhy dveřních klik,“ vysvětluje Pavel Karas, manažer oddělení vstřikování v závodě v Ostrově, během prohlídky výrobní haly. Pak dodává: „Kliky obsahující senzory a náležitá elektronická zařízení vyžadují instalační plochu s hladkou stěnou. Kvůli tomu vyrábíme kliky, kde mechanické šíbry uvnitř formy vymezují potřebné místo. Alternativou jsou kliky skládající se ze dvou nebo více částí, které drží pohromadě zaklapnutím a šrouby. Kliky bez integrované senzorové elektroniky mají jednodílné duté tělo vyráběné technologií vstřikování s podporou plynu,“ a zdůrazňuje, že „toto je nejefektivnější metoda k redukci tloušťky stěny výlisku, a tím pádem času potřebného ke zchlazení a spotřeby materiálu bez toho, aby musely být použity složité mechanismy uvnitř formy.“
Tento proces vypadá jednoduše, ale pro optimální výsledky je zapotřebí vysoce přesné kontroly procesu. Prvním krokem je kompletní naplnění dutiny a ztuhnutí vnějších vrstev chlazením stěny dutiny. Poté je vstřikovacími tryskami pod tlakem až 300 barů vstříknuta kontrolovaná dávka dusíku do plastové taveniny. Zde stlačený plyn působí jako píst, a vytlačuje ještě stále tekutou plastovou taveninu z vnitřku do přetokové dutiny skrze mechanicky otevřený kanál. V závislosti na druhu kliky tvoří množství vytlačené taveniny okolo 25–30 % celkového objemu. Stlačený plyn uvnitř nyní duté součásti následně zabraňuje smršťování při chlazení, tím pádem eliminuje možnost tvorby propadlin. Po dokončení chlazení je výlisek a obsah odtokové dutiny vyjmut, hmota z odtokové dutiny je následně odříznuta a recyklována, aby mohla být znovu použita s originálním materiálem (obr. 3). Čas jednoho cyklu je zredukován na 45–50 sekund podle modelu kliky, a tím pádem je zhruba stejný jako při procesu s použitím mechanických šíbrů.

Obr. 3: V současnosti je ve WITTE Ostrov vyráběno okolo milionu dveřních klik jako duté části PA6-GF 30. Obrázek ukazuje dva modely klik s jádrovým materiálem vytlačeným dusíkem do přetokové dutiny. Hotový produkt, klika připravená k instalaci se třemi vrstvami nátěru o vysokém lesku, je zobrazena uprostřed.
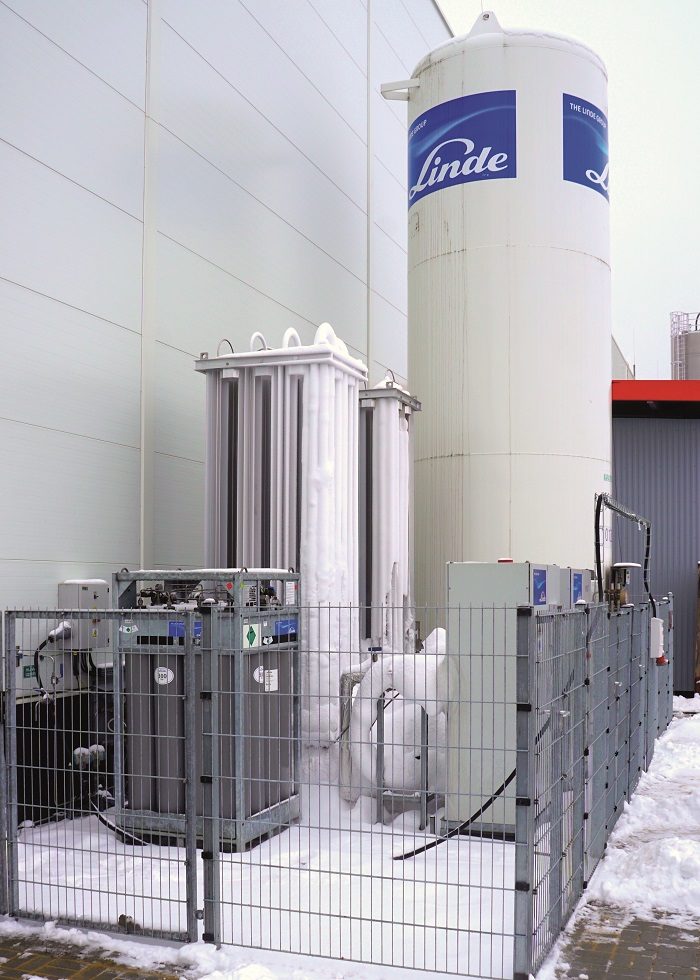
Obr. 4: Zařízení pro centrální zásobování dusíkem se skládá z nádrže tekutého dusíku propojené se dvěma vypařovacími jednotkami, z nichž každá je kombinovaná s kompresorem a baterií
plynových lahví pro stabilizaci systémového tlaku
Centrální síť tlakového dusíku pro všechny stroje
Když byla nová továrna postavena, byla veškerá infrastruktura pro vstřikování navržena jednak pro centrální zásobování strojů a jejich ovládání, ale také i pro budoucí modulární rozšiřování. Totéž platí pro elektrické napájení, systémy pro sušení a dopravu materiálu a pro zásobování dusíkem. Centrální zásoba a příprava dusíku i procesní jednotka se nachází mimo korporátní budovu. Centrální nádrž tekutého dusíku je v kombinaci se dvěma plynovými kompresorovými a odpařovacími jednotkami. Potrubní systém ve výrobní hale (obr. 4) s tlakem 300 barů je zásobován přes baterii plynových lahví pro vyrovnávání tlaku.
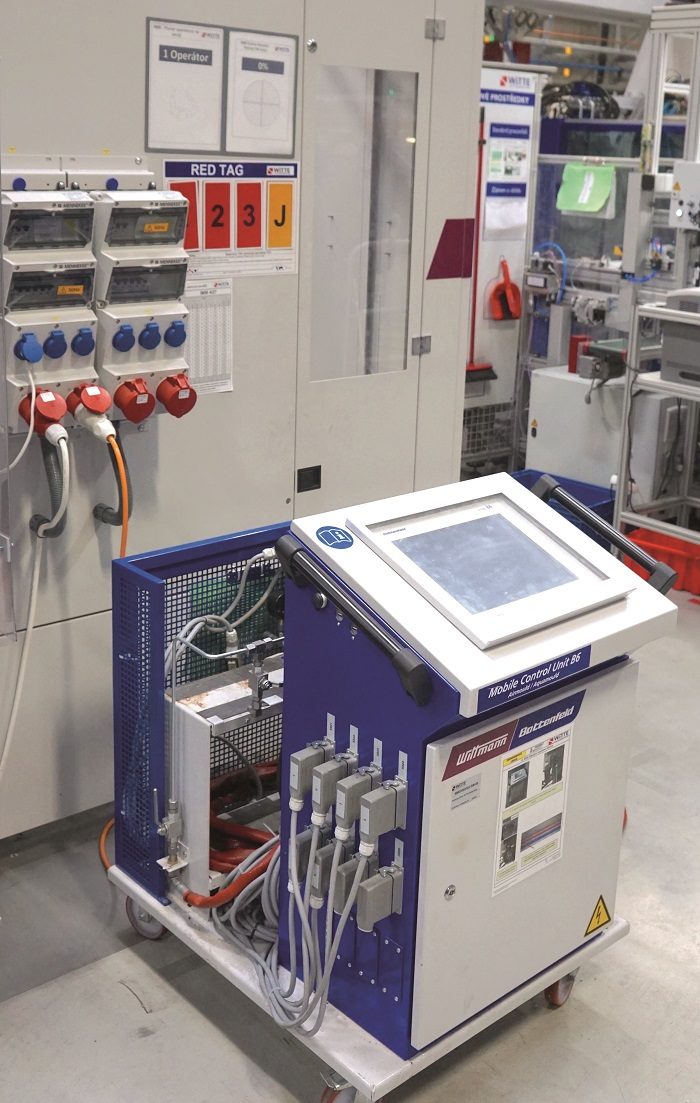
Obr. 5: WITTMANN BATTENFELD AIRMOULD® – řídicí systém schopný obsluhovat až osm regulačních modulů tlaku. Se stroji komunikuje přes rozhraní EUROMAP 62.
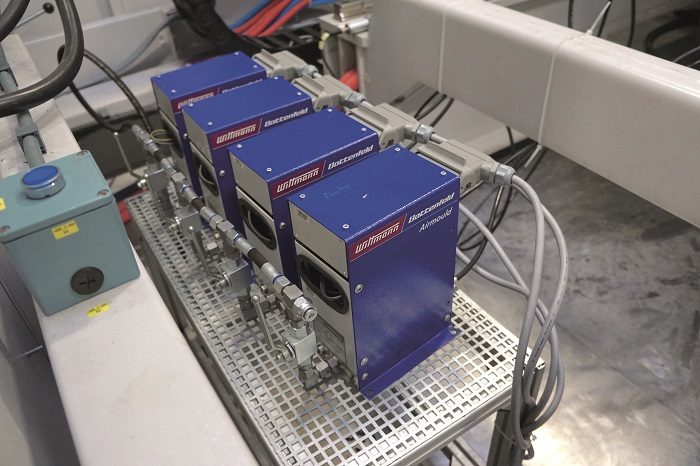
Obr. 6: Až na pár vyjímek jsou kliky vyráběny na 4násobných formách, kde je proud plynu na stroji
rozdělen do čtyř samostatných okruhů proudících přes samostatné regulační moduly tlaku.
Vysoký uživatelský komfort díky systémové integraci
Na vstřikovacích strojích je stlačený plyn rozváděn do několika samostatných trubiček vedoucích do vstřikovacích trysek uvnitř vstřikovací formy. Každá z těchto trubiček vede přes vlastní regulátor tlaku, který je ovládaný samostatnou řídicí jednotkou AIRMOULD®. Jedná se o samostatné zařízení, které může být flexibilně použito podle potřeby na několik strojů. Těžištěm mobilního řízení je jednotka UNILOG B6, kontrolní systém schopný obsluhovat až osm řídicích tlakových modulů a osm tahačů jader. Se vstřikovacím strojem komunikuje prostřednictvím standardizovaného rozhraní EUROMAP 62, speciálně navrženého pro integraci zařízení pro vstřikování fluidních materiálů. Na 15″ TFT‑barevné dotykové obrazovce řídicí jednotky AIRMOULD® mohou být zadány tlakové profily s nominálními křivkami a až devíti volně programovatelnými pozicemi. Je také možné zobrazit si aktuální tlakové křivky až u osmi řídicích tlakových modulů najednou. Dostupný je i vícekanálový monitorovací systém tlaku a impulsní program pro automatické čištění vstřikovacích trysek. Kontrolní jednotka AIRMOULD® zahrnuje ty samé základní funkce, jako řídicí systém stroje, jako autorizace přístupu pomocí USB nebo hesla a možnost ukládání procesních dat buď interně nebo externě přes USB nebo sítové připojení (obr. 5). Tlak plynu v jednotlivých trubičkách vedoucích k tryskám je regulovaný vysoce dynamickými servoventily, umístěnými uvnitř regulačních modulů tlaku. Aby se vyhnulo potenciálním ztrátám plynu a aby byla regulovaná sekce s plynem co nejkratší, jsou regulační moduly uvnitř stroje umístěny co nejblíže ke vstřikovací formě, ideálně přímo na upínací desce formy. Jelikož kromě pár výjimek jsou kliky vyráběny na 4násobné formě, je přívod plynu rozdělen do čtyř samostatných okruhů (obr. 6). Regulační moduly jsou navrženy s důrazem na vysokou přesnost regulace a kontroly velkého i malého množství plynu. Aby byla zajištěna stálá kvalita plynu, jsou regulační moduly vybaveny na vstupu i na výstupu plynovými filtry. Od regulačních modulů vedou jednotlivá plynová vedení do vstřikovací formy. (obr. 7).

Obr. 7: Pohled zblízka na 4násobnou formu produkující dveřní kliky technologií vstřikování s plynem.
Závěr
WITTMANN BATTENFELD již více než 30 let dodává zařízení pro sériovou výrobu silnostěnných jednokusových tvarově přesných výlisků bez propadlin. Díky strategickému rozhodnutí na vlastní vývoj může společnost nabízet integrované systémy ověřené při non‑stop provozech (24/7/365) ve výrobních závodech. Sám manažer výroby WITTE Pavel Karas spolupráci hodnotí pozitivně: „Vzhledem k naší pozici just‑in‑time dodavatele automobilových výrobců jsme naprosto závislí na permanentně spolehlivém výrobním zařízení. Zde jsme vždy těžili ze vstřikovací technologie společnosti WITTMANN BATTENFELD.“ (obr. 8)
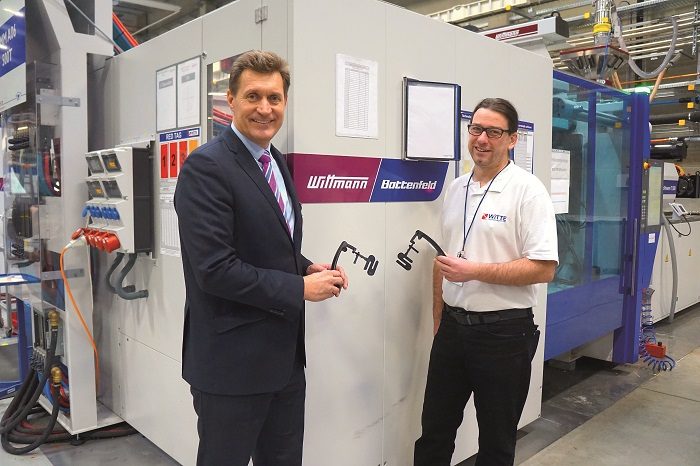
Obr. 8: Ing. Michal Slaba, jednatel WITTMANN BATTENFELD CZ a Pavel Karas, vedoucí výroby vstřikovaných dílů ve WITTE Ostrov, se společně ohlížejí na mnoho let úspěšné spolupráce
WITTMANN BATTENFELD je podnik skupiny WITTMANN s firemním sídlem a výrobou ve městě Kottingbrunn/Dolní Rakousko. Těžištěm podnikání je technika vstřikování plastových dílů a zastřešuje celou paletu strojů od zařízení pro mikrovstřikování s uzavírací silou 5 tun až po velké vstřikovací stroje s uzavírací silou 2 000 tun. Nabídku doplňují obsáhlé technologické pakety, např. pro vícekomponentní vstřikování, vstřikování strukturálních pěn a pojivových vláken. Ve spojení s možnostmi skupiny WITTMANN mohou být všechny vstřikovací stroje nabízeny včetně datových spojení ve smyslu Průmyslu 4.0.
Mohlo by se Vám líbit
Výroba kyčelních endoprotéz s pomocí měřicích strojů Hexagon a softwaru PC-DMIS
- Strojírenství
-
17. července 2025
Francouzská společnost Dedienne Santé se zaměřuje na výrobu implantabilních zdravotnických výrobků, zejména totálních náhrad kyčelních kloubů. Specializují se na tzv. náhrady s „dvojitou mobilitou“, kdy […]
DC napájecí konektory od firmy Amphenol GEC
- Elektro
-
16. července 2025
Řešení PowerLok™ navržená pro aplikace EV. Nabídka firmy TME byla rozšířena o zásuvky PowerLok™ od firmy Amphenol GEC. Jedná se o novou nabídku od renomovaného […]
Bezkontaktní monitorování frekvence a výkonu vysokofrekvenčního ultrazvuku
- Elektro
-
15. července 2025
Inovativní řešení APM od společnosti Ecoclean zajišťuje účinnost čištění megazvukem Monitorování frekvence a výkonu je důležitým nástrojem pro zajištění kvality ultrazvukového čištění v rozsahu 250 […]