07. září 2016 00:44
Produktivní zpětné zahlubování
Speciální nástroj od firmy Walter urychluje obrábění dílů při výrobě turbín
Čas jsou peníze. A v současné době nejen to. Neboť obchody narůstají jen těm firmám, které jsou rychlejší než konkurence. Pro zrychlení výroby proto stále více firem používá speciální nástroje. Berlínský závod na plynové turbíny divize Power and Gas společnosti Siemens tak výrazně zkrátil dobu obrábění součástí turbín: Od té doby, co firma používá plně automatický zpětný záhlubník Walter MODCO®, trvá vytvoření 16 zahloubení do příruby hřídele pro rotor plynové turbíny místo deseti hodin už jen 90 minut.
Dlouho nám bylo trnem v oku, že potřebujeme extrémní množství času na vytvoření zpětných zahloubení do určitých součástí,“ vzpomíná Markus Zapke, vedoucí skupiny technologie v závodě na výrobu plynových turbín v Berlíně. Vzhledem k dlouhým průběžným dobám a vysokému stupni vytížení strojů bylo podle Zapkeho přání „eliminovat tento takřka neřešitelný obráběcí problém“ stále naléhavější. Při hledání řešení se kompetentní pracovníci v roce 2012 obrátili na výrobce přesných nástrojů Walter, se kterým firma partnersky spolupracuje již déle než 25 let.
Obrovské díly pro velké plynové turbíny
Hřídele a kryty, které vyrábějí pracovníci v závodu na plynové turbíny ve výrobních halách v Berlíně na horizontálních vyvrtávacích a frézovacích strojích, mohou být velké jako autobusy. Tyto součásti se montují do turbín o výkonu až 400 MW. Ty se používají na celém světě pro výrobu energie v elektrárnách a v průmyslové oblasti. K uvedeným velkým součástem patří také hřídel rotoru CD-1. Přes 3,5 m dlouhá součást váží více než 13 t, její největší průměr činí téměř 1,5 m. Dutá hřídel je koncový díl (na straně kompresoru) rotoru 400 MW plynové turbíny SGT5-8000H, největší plynové turbíny na světě. Tato součást se připevňuje přírubou pomocí 16 čepů ke spojovací hřídeli, spojovacímu prvku s generátorem. To vyžaduje odpovídající velké množství průchozích otvorů (průměr 75 mm) do příruby o tloušťce přibližně 175 mm. Čepy se upevňují pomocí matic. Aby bylo pro matice místo, musí se u špatně přístupných vstupů vyvrtaných otvorů vytvořit zpětná zahloubení. Mají hloubku 56 mm a průměr 98 mm.
Jeden úkol trvající spoustu hodin
Hřídele CD1 se obrábějí v závodě na plynové turbíny v Berlíně v čtyřsměnném provozu na horizontálním vyvrtávacím a frézovacím stroji typu Škoda HCW 3 s příkonem 100 kW nebo na Pama Speedram 3 F s příkonem 50 kW. Stabilní stroje jsou všechny koncipované na obrábění objemných dílů. Spojují vysoký řezný výkon s vysokou přesností v celé pracovní oblasti. Přesto trvalo provedení jednoho zahloubení déle než 37 minut. Hřídele jsou z materiálu 26NiCrMoV14-5. Tato nízkolegovaná ocel s nízkým obsahem uhlíku se vyznačuje velmi dobrými mechanickými a tepelnými vlastnostmi. Typicky se používá pro vysoce namáhané součásti v energetické oblasti a dále ve všeobecném strojírenství. „Protože tento tepelně zpracovaný materiál má relativně vysoký obsah niklu, je skutečně houževnatý a jeho obrábění není úplně jednoduché,“ ví Ralf Hohendorf, technolog v závodu na turbíny v Berlíně. „To ztěžuje vytváření otvorů a zahloubení.“ Společnost Siemens PG k tomu dlouho používala zpětný záhlubník, který se musel manuálně osazovat dvoubřitým HSS nožem. S tímto nástrojem trvalo vytvoření jednoho zahloubení téměř 16 minut. Včetně pomocných časů, například na odstranění třísek, činil potřebný čas více než 37 minut. Na 16 zahloubení u jednoho obrobku byla tedy zapotřebí doba obrábění celých deset hodin.
Automaticky místo ručně
S takovou spotřebou času se odpovědní pracovníci nechtěli smířit. Poradili se s odborníky pracujícími pro Walter Německo Michaelem Hartschem, zodpovědným za technické poradenství a prodej pro klíčové zákazníky, a dále Stefanem Rißmannem, aplikačním technikem pro klíčové zákazníky. Tito dva odborníci na obrábění navrhli řešení: zpětný záhlubník Walter MODCO® osazený vyměnitelnými břitovými destičkami. „Tento plně automatický speciální nástroj má s 250 mm stejnou délku vyložení jako doposud používaný nástroj,“ vysvětluje Michael Hartsch. „Ale na rozdíl od něj má vnitřní chlazení.“
Jakmile projde nosný nástroj otvorem v přírubě, může začít rotační zpětné zahlubování. To probíhá pomocí dvou ramen, která jsou zapuštěná v přední části nosného nástroje a automaticky se vyklápějí na stranu. Protilehlá ramena jsou osazená vždy jednou dvoubřitou speciální destičkou ze slinutého karbidu. Boční vyklápění a zaklápění je řízené tlakem vnitřního chlazení. Manuální zásah je zbytečný. „U dosavadního řešení musela obsluha dvoubřitý HSS nůž obtížně nasadit do držáku a zafixovat ho,“ poznamenává Stefan Rißmann.
Časová úspora předčila očekávání
Nástroj od firmy Walter byl nejprve otestován na litinových krytech a poté na hřídeli CD-1. „Od konce roku 2015 probíhá obrábění podle přání,“ potvrzuje Markus Zapke. „Hřídele lze bez problémů a spolehlivě obrábět bez další podpory a nástroj je schválený pro výrobu.“
Zpětný záhlubník ze slinutého karbidu vytvoří jedno zahloubení za 67 sekund. Včetně pomocných časů trvá celý proces již jen přibližně 5,5 minuty. To odpovídá přibližně pouhým 15 procentům předtím potřebného času. „S takovou časovou úsporou jsme ani nepočítali,“ prozrazuje Ralf Hohendorf. Díky výrazně lepšímu výkonu lze 16 zahloubení u jednoho dílu s nástrojem Walter nyní provést za 1,5 hodiny. To představuje zkrácení celkové doby obrábění na 15 %. Navíc to přináší úsporu v dolním rozsahu pětimístného řádu v eurech.
Nutný jen malý počet řezných nástrojů
Závod na turbíny v Berlíně kromě toho zaznamenal dlouhou životnost vyměnitelných břitových destiček ze slinutého karbidu od firmy Walter. Ralf Hohendorf: „Se speciálním nástrojem od firmy Walter můžeme nyní plynule obrábět dvě součásti, a tedy přesně minimální dávku.“ HSS nůž dříve používaného zpětného záhlubníku byl naproti tomu opotřebený již po jednom zahloubení a musel se vyměnit. Zatímco tedy bylo u 16 součástí nutné naostřit celkem 256 HSS nástrojů, alternativně se použije pouze osm vyměnitelných břitových destiček ze slinutého karbidu. „Díky podstatně menšímu opotřebení se náklady na naše vyměnitelné břitové destičky ve srovnání s HSS nožem rychle amortizují,“ vysvětluje Michael Hartsch. Ohledně nastavení nástroje vyplývají pro Siemens PG výrazné úspory: Při odhadovaných deseti minutách na externí nastavení činí celková doba u nového nástroje s osmi opotřebenými vyměnitelnými destičkami pouze 80 minut – to je pouze zlomek toho, co bylo zapotřebí u dosavadního nástroje s 256 použitými HSS noži. Pokud vycházíme z hodinové sazby v prostředním rozsahu dvoumístného řádu v eurech, jsou tyto náklady u řešení od firmy Walter srovnatelně nižší, zatímco u dosavadního řešení byly ve čtyřmístném řádu.
Jednoduché, rychlé a efektivní
Kompletní nosný nástroj od firmy Walter s plně automaticky řízenou mechanikou stojí sice více než dříve používaný manuální nosný nástroj, ale tyto náklady se zaplatí ani ne za rok. „Kromě toho má takový nosný nástroj dlouhou životnost,“ říká Markus Zapke. „Jen se občas musí vyměnit vodicí pouzdra.“ Ale nezamlčuje ani to, že při manipulaci s novým nástrojem a použití, stejně jako při údržbě, je zapotřebí určitý trénink a vysoká pečlivost.
Výrobní expert vyvozuje pozitivní bilanci: „Nový, automatizovaný systém se vyznačuje podstatně jednodušší manipulací a obsluhou než ten dříve používaný a průběžný čas je nyní výrazně kratší. K tomu se přidává skutečnost, že je dosahováno výrazně lepší jakosti povrchu než s předcházejícím nástrojem.“ Celý projekt probíhá podle Zapkeho natolik pozitivně, že se uvažuje o používání nástroje od firmy Walter také pro další součásti. A ještě něco nezapomene inženýr zmínit: „Spolupráce s odborníky z firmy Walter je přesně taková, jak jsme si to přáli.“
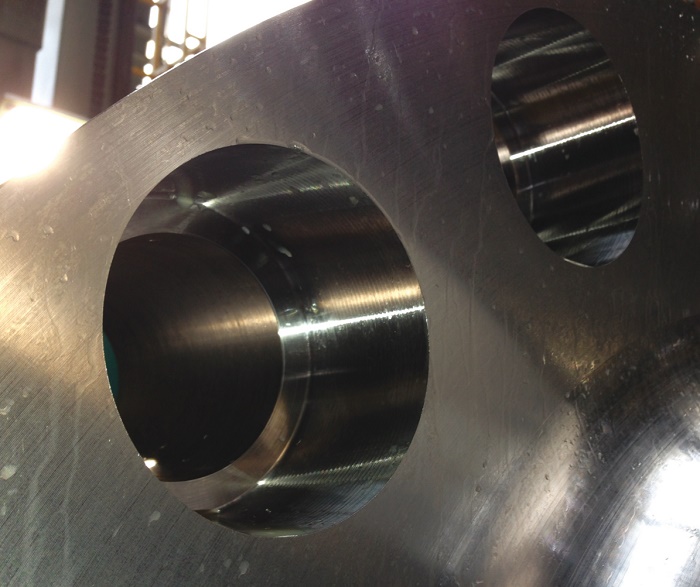
Zahloubení na zadní straně hřídele CD-1 mají hloubku 56 mm a průměr 98 mm (foto: Siemens)
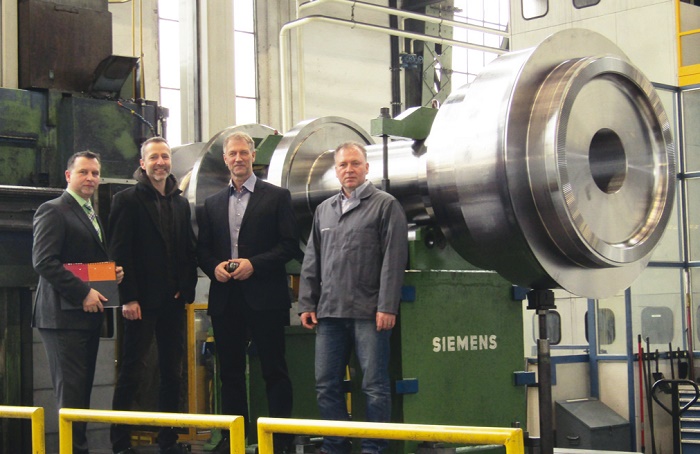
Spolupracující partneři před upnutou dutou hřídelí CD-1 (zleva): Michael Hartsch z firmy Walter, Markus Zapke a Ralf Hohendorf z firmy Siemens PG a Stefan Rißmann z firmy Walter (foto: Reichenbach)
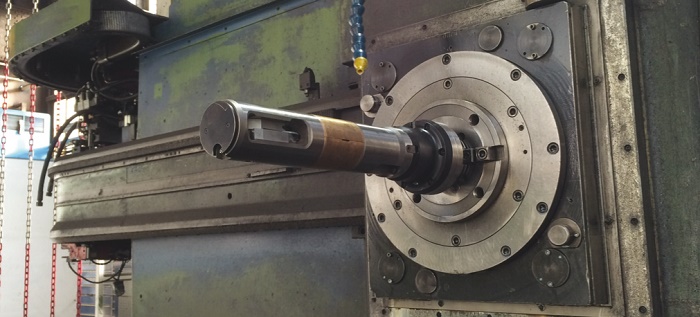
Zpětný záhlubník ze slinutého karbidu, upnutý na vyvrtávacím a frézovacím stroji, má délku vyložení 250 mm (foto: Siemens)
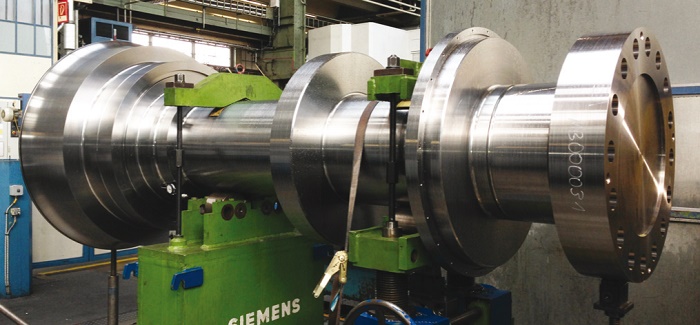
Příruba tepelné hřídele CD-1 je opatřená 16 otvory a zahloubeními (foto: Siemens)
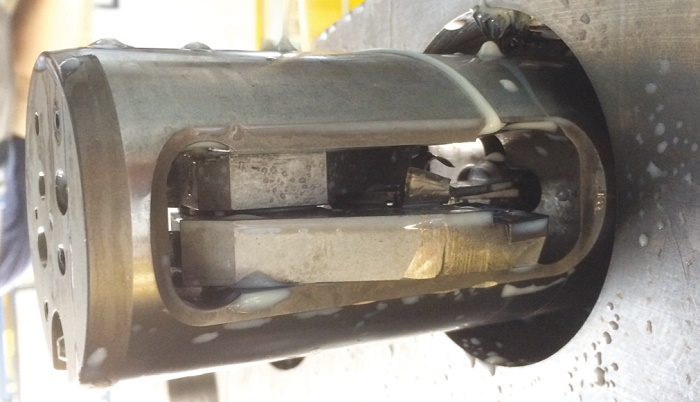
Zpětný záhlubník ze slinutého karbidu s vnitřním chlazením Walter MODCO®
při vytváření zahloubení do příruby hřídele turbíny typu CD-1 (foto: Siemens)
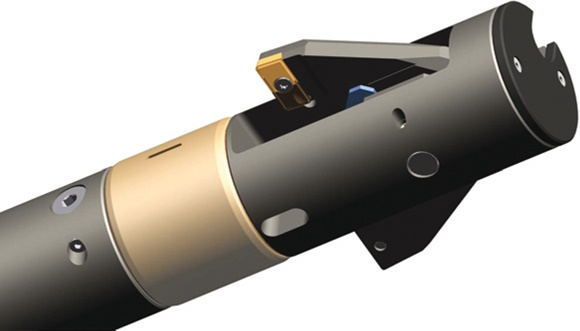
Zobrazení nástroje se zasunutými, resp. vysunutými noži (foto: Walter AG)
Mohlo by se Vám líbit
Cílem je stát se jedničkou pro oblast kabelů
- Elektro
-
10. července 2025
Společnost KONEKA, která vznikla vloni na podzim jako dceřiná společnost PRAKAB (PRAKAB Pražská Kabelovna s.r.o.), plánuje v letošním roce dále rozšiřovat své služby a produktové portfolio. […]
Každý den je jinak BAREVNÝ!
- Plasty
-
08. července 2025
Chcete si pověsit na zeď něco barevného a užitečného? Připravili jsme pro Vás nový plakát se základními informacemi o barevném prostoru CIELab a výpočty ΔE […]
Nové elektrické polohovací zařízení HIWIN: Spolehlivý a přesný lineární pohyb
- Automotive
-
08. července 2025
Jedinečné na trhu díky přídavnému podpůrnému vedení HIWIN, přední výrobce lineárního vedení, kuličkových šroubů a polohovacích zařízení, představil na letošním veletrhu Automatica 2025 v Mnichově […]