06. června 2016 00:48
Přínosy CAM a vysokorychlostního frézování výrobě zápustek a forem
Výroba zápustek a forem byl tradičně dlouhý, obtížný a drahý proces, vyžadující hluboké technologické znalosti a zkušenosti. S dnešním pokrokem CAM softwaru se zhotovení zápustky a formy racionalizovalo. Není již třeba tak vysoké odbornosti, proces je předvídatelný a výrobce ušetří mnoho času i peněz.
Obvykle se ve výrobě forem (nebo zápustek) používají dvě technologie:
- První postup spočívá ve vyhloubení dutiny formy do předem zakaleného bloku oceli elektro -erozivním způsobem (EDM), pomocí grafitových nebo měděných elektrod, které byly předem vyrobeny jako negativy požadovaného tvaru dutiny. Po vyhloubení dutiny následuje její dokončovací obrobení.
- Druhým tradičním postupem se dutina přímo obrobí do nezakaleného ocelového bloku, blok se teprve potom zakalí, a pak začíná dlouhý a svízelný úkol dokončení formy.
K vytvoření CNC programů, s jejichž pomocí se strojně vytvoří požadovaný tvar formy, se používají CAM systémy. CAM systém přebírá geometrický model formy vytvořený v nějakém CAD systému, ale v případech, kde CAM je integrován do běžného CAD systému, pracuje se s CAD modely jako s vlastními modely, bez nutnosti jejich přenosu. V takových integrovaných CAM systémech se hlavní úspory realizují vždy, když se požaduje modifikace tvaru či geometrie formy. Tím, že se udělají nezbytné změny přímo v CAD modelu, změní se automaticky celá návazná geometrie formy a CNC dráha nástroje se automaticky aktualizuje, pokud jsou přiřazeny CAM operace, které definují pořadí a typ obráběcích strategií a jejich vztah ke geometrii formy.
Vysokorychlostní frézování – zvláštní výhoda v CAM
Existuje nová technologie vysokorychlostního frézování propojená s CAM, která redukuje čas a náklady obrábění forem nejméně na 50 % a produkuje mnohem přesnější formu s životností milionů pracovních cyklů. Tato technologie se dodává pod chráněnou značkou iMachining. Byla vytvořena izraelskou společností SolidCAM (obr. 1).
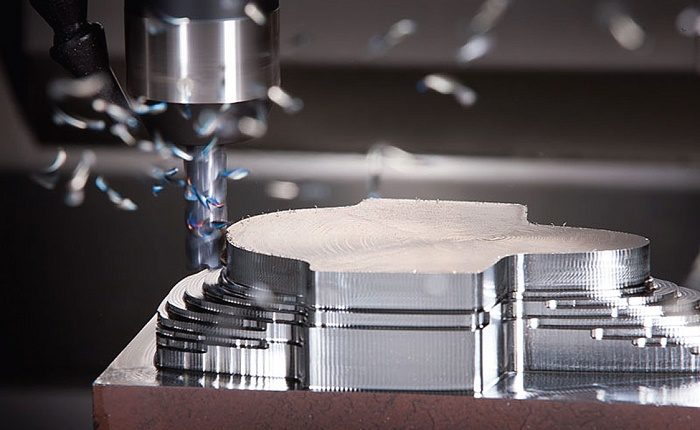
Obr. 1: Vysokorychlostní frézování pomocí systému 3D iMachining
Pomocí technologie iMachining je možné vytvořit dráhu nástroje, která umožňuje vyrábět na běžných, středně velkých frézovacích strojích dutiny forem přímo do oceli kalené na tvrdost 62 HRC a výše. To je hlavní výhoda oproti tradičním CAM systémům. Přesnost a jakost povrchu, které lze pomocí dráhy nástroje generované v iMachining docílit, je udivující. Před použitím formy je třeba již jen minimální ruční leštění.
Není třeba odstraňovat žádná vyhřátá místa, žádné zborcení tvaru formy v důsledku vnitřního pnutí uvolněného při agresivním obrábění, nevytvoří se žádné mikro-trhliny, které snižují životnost formy. Forma je obrobena na finální rozměry s vysokou jakostí povrchu a ručním leštěním je třeba odebrat jen minimum materiálu (v závislosti na přesnosti frézovacího stroje).
Vysokorychlostním frézováním technologií iMachining se docílí takovéto přesnosti tím, že se používají malé řezy. Tloušťka třísky je typicky asi 0,5 až 2 % průměru nástroje. A většinou ještě méně ve velmi tvrdých materiálech. Používají se vysoké posuvové a řezné rychlosti. Podél dráhy nástroje se udržuje konstantní mechanické i termální zatížení nástroje, jak jen to je možné. Aby se toho docílilo, je třeba usilovat o udržení stálých podmínek řezání nástroje. Strategie dráhy nástroje, která slibuje nejdelší kontinuální řezání, je monotónní spirálová dráha (divergentní nebo konvergentní), viz obr. 3.
Jelikož reálné obrobky a formy mají nepravidelné tvary a různé izolované útvary, budeme je nazývat „ostrovy“, je obecně nemožné odebrat všechen materiál, který je potřeba odřezat, jednou souvislou spirálou. Většina systémů, které používají vysokorychlostní frézování ve spojení s CAM, využívá trochoidální dráhu nástroje k odebrání veškerého materiálu z dutiny formy. V systému iMachining je variantou trochoidální dráhy tzv. D-typ dráhy, viz obr. 3.
Celý systém by měl být natolik inteligentní, aby analyzoval tvar té části dutiny formy, která má být právě vyfrézována, měl by být schopen rozdělit ji do několika oddělených oblastí, pak, s použitím kvazi-trochoidální dráhy nástroje (D-typ dráhy), proříznout oddělovací kanály a obrobit každou z těchto oblastí s nesymetrickou spirální dráhou nástroje. Oddělovací kanály obvykle zabírají malé procento celkové plochy, která má být obrobena, což znamená, že většina plochy je obrobena spirálovou dráhou, a to je dvakrát efektivnější než obrábění pomocí trochoidální dráhy nástroje.
Systém iMachining s technologickým průvodcem
Nový systém iMachining je propojen s Technologickým průvodcem. Ten obsahuje sofistikovaný matematický model všech proměnných veličin obrábění a jejich vzájemné závislosti. Když je postaven před úkol něco obrobit, což zahrnuje cílovou geometrii obrobku a výchozí geometrii polotovaru, nástroje, materiál a údaje o stroji, nalezne Technologický průvodce optimální řezné podmínky pro vysokorychlostní obrábění celého obrobku.
Je třeba poznamenat, že Technologický průvodce není nějaký soubor předem vypočtených tabulkových parametrů. Průvodce provádí složité iterativní, optimalizační výpočty s cílem získat hodnoty řezných parametrů, kterými se rychle, bez chvění a s konstantním zatížením bude obrábět, přičemž se berou v úvahu omezení stroje, cílová geometrie, materiál obrobku a nástroj.
Kromě toho, jelikož je obecně nemožné udržet konstantní posuv v celém řezném procesu, neboť existují limity zrychlení a zpomalení stroje na malých obloucích dráhy nástroje apod., Technologický průvodce disponuje algoritmem generování dráhy nástroje vybaveným odpovídajícími rovnicemi, které dovolují přesné přizpůsobení rychlostí a zanoření nástroje do materiálu v každém bodě dráhy nástroje.
S použitím řezných podmínek vytvořených Technologickým průvodcem, Automatický generátor dráhy nástroje spočítá všechny dráhy nástroje potřebné k účinnému obrobení formy, od dané geometrie polotovaru k cílové geometrii, při požadované kvalitě konečného obrobeného povrchu. Příklad vidíme na obr. 2. V místech 1, 8, 10 jsou vytvořeny tvarované spirálové dráhy nástroje. V místech 2 a 9 je použita kvazi trochoidální dráha nástroje (D-typ). Drážky a tzv. příkopy 3, 4 a 5, oddělující jednotlivé útvary formy, se rozšiřují s použitím tzv. klobásového tvaru dráhy. V místech 6, 7 se vytvoří uzavřené konkávní oblasti.
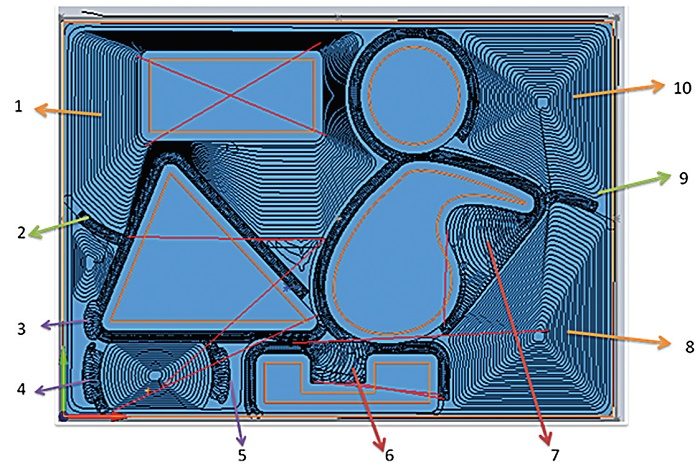
Obr. 2: Dráhy nástroje
Nejprve Automatický generátor dráhy nástroje vypočte dráhy pro hrubovací řezy, které provedou algoritmy nazvané „Rough Cut“– hrubování a „Rest-Rough“– hrubé frézování „schodů“ zbylých po hrubování. V obou případech se frézuje nástrojem s největším vhodným průměrem a s plochým koncem.
Rough Cut používá dva základní typy dráhy nástroje:
- tvarovanou spirálovou dráhu nástroje,
- modifikovanou trochoidální dráhu nástroje zvanou D-Typ.
Tvarovaná spirálová dráha nástroje je takto nazývána proto, že na rozdíl od spirálových drah ve většině systémů vysokorychlostního frézování (HSM-CAM) tvarovaná spirálová dráha nástroje postupně přijímá tvar oblasti, kterou má odfrézovat (obr. 3 vlevo), místo aby symetricky expandovala jako kruhová spirála na obr. 3 vpravo. Tato schopnost podstatně redukuje dobu obrábění.

Obr. 3: Křivky použité na dráhu nástroje
Na obr. 3 vlevo je vidět, že silně tvarovaná spirála s různým stoupáním v osách X a Y vyplní celou plochu, která se má odfrézovat, aniž by byla přerušena. Naopak, jen slabě tvarovaná spirála je téměř kruhová a vyplní jen část plochy (obr. 3 vpravo). Zbytek musí být odfrézován pomocí trochoidální dráhy. Ta je modifikována v části vratných přejezdů a připomíná písmeno D. Proto název D-Typ.
Ideálně bychom chtěli celou plochu, která se má obrobit na určité úrovni Z osy, ofrézovat jednou souvislou spirálovou dráhou nástroje. Obecně to není možné. Hrubovací algoritmus proto rozdělí celou plochu na optimální počet dílčích ploch, z nichž každá může být obrobena tvarovanou spirálovou dráhou, tak aby celková doba obrábění byla minimální. Algoritmus použije D-Typ dráhy nástroje k vyfrézování drážek, kterými se celá plocha rozdělí. Viz obr. 4, obr. 5 a obr. 6.
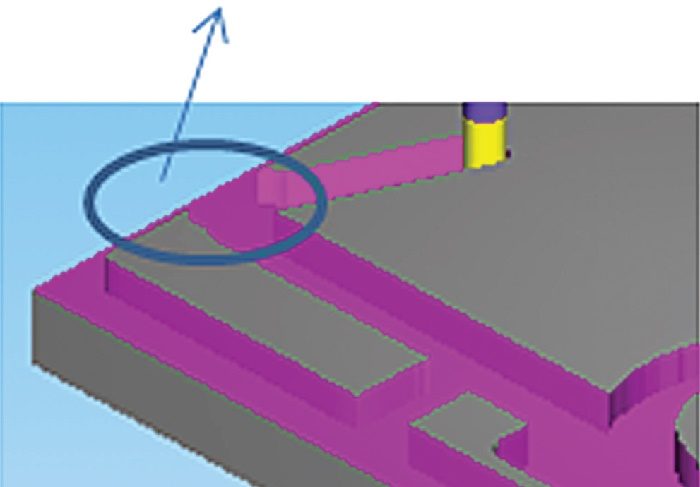
Obr. 4: Eliminace tenké stěny
Obr. 4 ukazuje, jak „klobásové“ rozšíření „příkopů“ eliminuje tenkou stěnu, která by zůstala mezi příkopem a hranou materiálu.
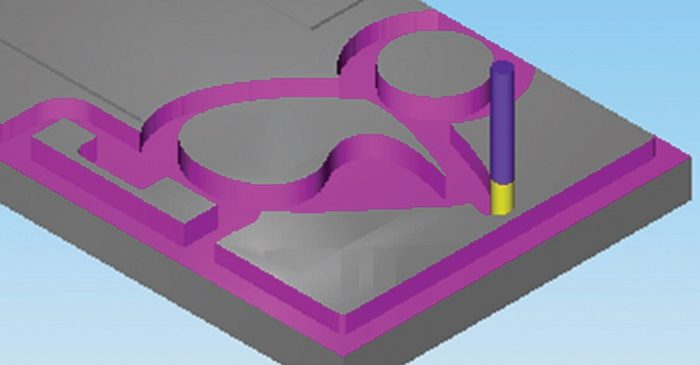
Obr. 5: Nepravidelná plocha nevhodná pro spirálovou dráhu nástroje
Na obr. 5 vidíme detail součásti z obr. 2. Program, po vyfrézování příkopů kolem tří ostrovů, rozpozná, že plocha, která byla oddělena, je příliš nepravidelná, aby mohla být frézována tvarovanou spirálou, a automaticky rozhodne rozdělit plochu oddělovací drážkou. Na obr. 6 již vidíme dvě pravidelnější plochy A, B, vhodné pro tvarovanou spirální dráhu, rozdělené drážkou C.
Další unikátní a důležitou výhodou Hrubovacího algoritmu je fakt, že v každém bodě podél vytvořené dráhy nástroje jsou hodnoty tloušťky třísky, posuvu a otáček vřetena vždy přizpůsobovány situaci podle optimalizačních pravidel stanovených Technologickým průvodcem. Přesným nastavováním řezných podmínek, spojeným s optimálním rozdělením frézované plochy, je umožněno, že již první vyrobený obrobek je bezchybný. Kromě toho je na obvyklém, středně velkém obráběcím centru, vyroben s časovou úsporou 40 až 70 %.
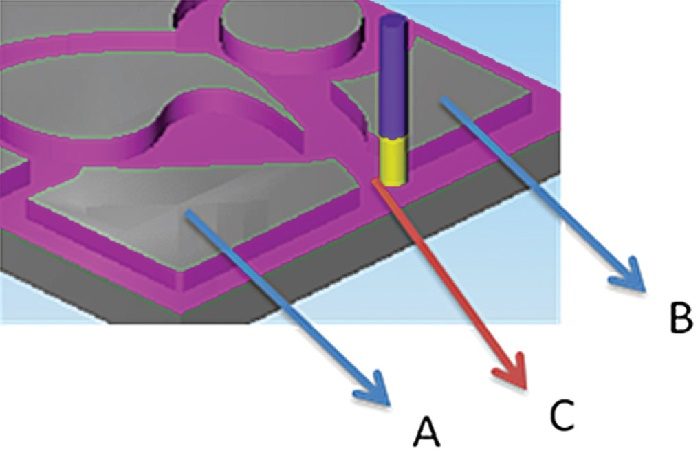
Obr. 6: Rozdělení nepravidelné plochy
Speciální algoritmus, nazvaný Rest Rough hrubuje materiál zbylý po obrábění pomocí Rough Cut. Používá se rovněž hrubovací nástroj. Program Rough Cut odfrézuje většinu materiálu z nějaké kapsy nebo kolem nějakého „ostrova“ (výčnělku). Jelikož používá poměrně velký krok při zanořování do materiálu, vytváří velké stupně na šikmém povrchu, jejichž příklad vidíme na obr. 1. Úkolem algoritmu Rest Rough je tyto stupně odstranit. Rest Rough navede nástroj tak, že ten začne stoupat vzhůru a frézuje pouze, když je to třeba, aby snížil velikost stupňů na požadovaný limit. Rest Rough zabrání přejezdům nástroje v kapse na ostatní vzdálené šikmé stěny, dokonce i tehdy, když je nástroj potřebuje také obrobit. Jakmile nástroj dokončí obrábění při pohybu vzhůru, sjede opět dolů a začne frézovat stupňovitý tvar na ostatních šikmých stěnách kapsy směrem vzhůru. Tímto postupem je minimalizována doba přejezdů nástroje.
Shrnutí
Výroba forem na zpracování plastů je a bude nejvýznamnějším trhem pro 3D HSM-CAM. Zde jsou důvody pro toto tvrzení:
- Frézování dutiny formy přímo do zakaleného bloku nástrojové oceli s vysokou kvalitou obrobeného povrchu má, při použití technologie iMachining, šest hlavních výhod pro výrobce formy:
- Mnohem kratší dobu obrábění.
- Bezobslužné obrábění.
- Žádné tepelné deformace – protože řezy jsou mnohem méně agresivní, řezné síly jsou mnohem menší než při klasických frézovacích technologiích, výsledný geometrický tvar formy je mnohem méně zborcený od uvolněných vnitřních napětí, dokončovací řez je mnohem blíže finálním dimenzím a tvaru formy a povrch dokončené formy nemá téměř žádná zbytková napětí.
- Mnohem méně manuálního dokončování a leštění formy.
- Lepší konečnou rozměrovou přesnost formy.
- Forma nemá mikrotrhliny, takže je kvalitnější a má vyšší životnost.
- Na globálním trhu elektroniky, přístrojů, spotřebičů a dokonce i hraček existuje trend stále větších požadavků na varianty modelů. Každý chce jiný model, než mají přátelé a sousedé. Výsledkem je to, že výrobci musí vyrábět mnohem více forem než dříve. Tento trend rychle roste, což znamená, že tržní podíl výroby forem musí také růst rychle.
- Rychlost, se kterou nové termoplastické polymery, vždy s lepšími vlastnostmi, opouštějí laboratoře, roste exponenciálně. Následkem toho roste exponenciálně i rychlost, s jakou jsou výrobky, dříve zhotovované z kovu nebo dřeva, rekonstruovány na výrobky plastové.
- Můžeme proto věrohodně soudit, že:
- Globální trh vstřikovacích forem na plasty bude pokračovat v růstu ještě po nějakou dobu.
- Sofistikované technologie nejpokročilejších 3D HSC, jako je iMachining, nabízejí výrobcům nejlepší alternativu s následujícími přednostmi:
- Technologický průvodce, založený na znalostní databázi, automaticky vypočítává optimalizované řezné podmínky, takže již první výrobek je bezchybný.
- Spirální frézování dokonce i nepravidelných ploch. Mnohem delší životnost nástrojů.
- Řízené zatížení nástroje v každém bodě podél dráhy nástroje, což vede opět na dlouhou životnost nástroje.
- „Ostrovy“ (výstupky či izolované útvary ve formě) jsou obklopeny „příkopy“ (rozšířenými drážkami), aby se umožnilo souvislé frézování spirálovými řezy, dokonce i v případech násobných ostrovů. Také toto prodlužuje životnost nástroje.
- Automaticky se zamezuje vzniku tenkých stěn.
Michael Berman,
hlavní vědecký poradce firmy SolidCAM pro technologii iMachining, Izrael
Mohlo by se Vám líbit
Na trh vstupuje soudkovitá fréza CoroMill® Plura barrel – řešení, s nímž se tvarové obrábění posouvá o další krok vpřed
- Obrábění
-
04. července 2025
Společnost Sandvik Coromant zařadila do své nabídky novou koncepci monolitních karbidových stopkových fréz, která umožňuje zkrácení času cyklu až o 90 %. Inzerce Společnost Sandvik Coromant, která […]
Přípravy na MSV 2025 jsou v plném proudu. Podívejte se na první novinky letošního ročníku
- Strojírenství
-
03. července 2025
Od 7. do 10. října 2025 se na brněnském výstavišti koná již 66. ročník Mezinárodního strojírenského veletrhu. Svým návštěvníkům představí průmyslové inovace a nejnovější trendy napříč obory. Letos se […]
Bez mazání i při použití kovu: Polymerová kuličková ložiska pro nápojáře
- Strojírenství
-
02. července 2025
Samomazná a bezúdržbová kloubová ložiska igubal nově dostupná s cenově výhodnými plechovými domečky V nápojářském průmyslu jsou ložisková tělesa a přírubová ložiska často vystavena silnému […]