06. června 2016 00:23
Jak využít dynamiku frézovacího procesu ke zvýšení řezného výkonu
Mezi frézaři je známo, že nástroj se při určitých řezných podmínkách intenzivně rozkmitá. Odborně říkáme, že proces obrábění je nestabilní. Kmitání je provázeno nepříjemným hlukem, často na vysoké frekvenci. Na povrchu obrobku se objeví více méně pravidelné vlny. Jelikož je oprávněná obava, že kmity poškodí nástroj, musí se obrábění přerušit a najít jiné řezné podmínky. Často je to zdlouhavé hledání. Obvykle je nakonec nutné snížit axiální, případně i radiální hloubku řezu a také změnit řeznou rychlost. Vyskytnou-li se kmity během obrábění jiného obrobku, opakuje se stejná situace.
Úvod
V tomto článku nabízíme nejen stručné vysvětlení, o jaké kmitání se v takových případech jedná, ale hlavně metodu, jak jednoduchými řeznými zkouškami získat informace, které pomohou kmitání snížit a někdy i zcela odstranit. Dokonce je možné i zvýšení řezného výkonu nástroje, čili zvýšení úběru třísek, což se může hodit např. při frézování hlubokých forem, kde může být výhodné frézovat velkými axiálními hloubkami řezu.
Aby bylo naše vysvětlování srozumitelné a aby nevznikly později při praktické aplikaci nejasnosti, je třeba nejprve absolvovat krátký kurz, v němž bez velké teorie vysvětlíme, co je to „dynamická poddajnost stroje“ a „diagram stability“. Ukážeme, jak se teorie využívá pro potlačení kmitů při obrábění. Nevyhneme se přitom jednoduché mechanice a matematice, ale budeme se snažit o co nejpřístupnější vysvětlení teoretických pojmů. Kdo se však nechce teorií zdržovat, může skočit na odstavec „Diagram stability řeznou zkouškou“, kde jsou praktické rady, jak zjistit řezné podmínky bez chvění (stabilní řezné podmínky).
Dynamická poddajnost stroje
Skutečný obráběcí stroj, včetně nástroje a obrobku, kmitá při obrábění ve třech směrech a některé části stroje se mohou při kmitání i natáčet. Tento složitý mechanický systém zjednodušíme a nahradíme ho kmitavým systémem, který může kmitat jen v jednom směru. Říkáme, že model stroje má jeden stupeň volnosti. K jeho matematickému popisu stačí jedna rovnice. Model vidíme na obr. 1.
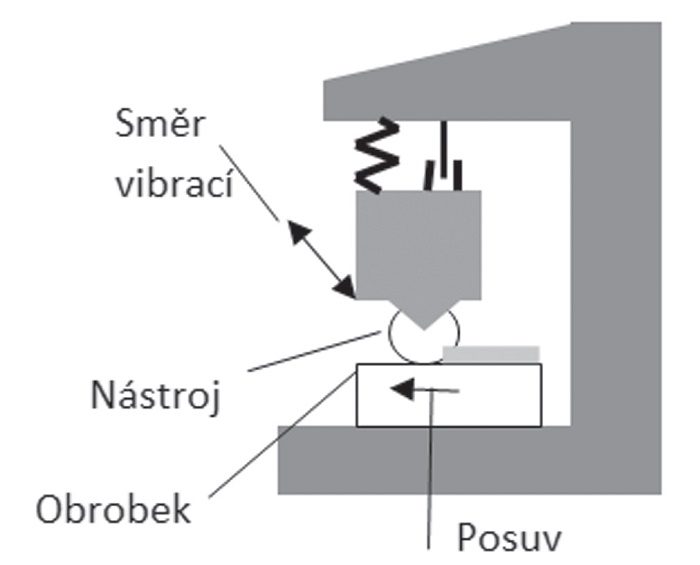
Obr. 1: Zjednodušený model frézovacího stroje
Chceme ukázat, že s tímto jednoduchým modelem se dají získat prakticky použitelné výsledky, které zlepšují řezný výkon stroje. Model sestává z pružiny o jisté statické tuhosti k, z viskózního tlumiče, jehož tlumící konstanta je označena C, a z ekvivalentní hmoty M. Kmity při obrábění jsou vyvolány jistou budicí silou F. Po celou dobu kmitání musí být budicí síla F v rovnováze se silou pružiny k ∙ x = k ∙ X ∙ sin(ωt), silou tlumiče C ∙ = C ∙ X ∙ ω ∙ cos(ωt) úměrnou rychlosti kmitání a se setrvačnou silou
M ∙ = M ∙ X ∙ ω2 ∙ (-sin(ωt))
úměrnou zrychlení kmitavého pohybu.
Protože tyto síly jsou periodické, kmitavé, jsou znázorněny sinusovými funkcemi, resp. kosinovou funkcí. Ve vztazích značí ω[1/s] úhlovou rychlost, čili rychlost rotačního pohybu, takže součin ωt dává úhel a má význam úhlové polohy nějakého vektoru. Představujeme si, že např. síla C ∙ = C ∙ X ∙ ω ∙ cos(ωt) rotuje v čase t úhlovou rychlostí ω, stejně jako ostatní vektory sil. Takovému rotujícímu vektoru říkáme fázor a chceme tím zdůraznit důležitost vzájemných úhlových, neboli fázových, poloh jednotlivých sil. Obraz těchto fázorů promítnutý do směru vibrací vytváří pak sinusovku vibračního pohybu. Ve shora uvedených vztazích jsou síly odporující budící síle vyjádřeny jako sinusové funkce s patřičným fázovým posunutím. Je zde patrné, že násobek ω a ω2 vznikl derivací funkce sin(ωt).
Rotující vektory sil, resp. fázory, lze znázornit komplexními čísly. Na rozdíl od reálných čísel, která mohou znázornit jen jednu hodnotu, komplexní čísla udávají hodnoty dvě. Mají reálnou a imaginární část. Mohou tedy zobrazit koncové body fázorů vibrací. Reálná část komplexního čísla se obvykle přiřazuje vodorovné ose komplexní roviny, imaginární část se přiřazuje vertikální ose. Imaginární složka není nereálná. V matematické terminologii přívlastek „imaginární“ označuje směr kolmý k reálné ose, která se obvykle kreslí vodorovná. Reálná osa má jednotku 1, imaginární,
, kde písmeno j značí imaginární jednotku.
Příkladem jsou fázory sil na obr. 2. Deformace pružiny X a síla pružiny k ∙ X jsou reálné a kladné. Síla je ve fázi s deformací pružiny. Setrvačná síla je také reálná, ale negativní, fázově tedy předbíhá sílu pružiny o 180°. Tlumící síla je imaginární, nemá reálnou složku a předbíhá sílu pružiny o 90° díky funkci cos. Kmitavá budicí síla je komplexní. Její velikost F i fázi lze vypočítat z rovnováhy sil. Všechny vektory sil rotují v komplexní rovině, dané reálnou a imaginární osou, a zachovávají si svůj fázový posun. Je zřejmé, že komplexní čísla jsou velmi vhodná pro řešení a znázornění vibračních úloh.
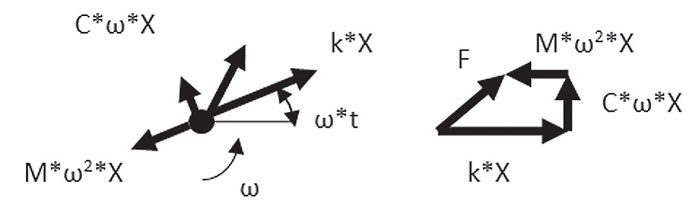
Obr. 2: Fázory sil. Vlevo fázory, vpravo rovnováha sil
Rovnováha sil nakreslená na Obr. 2 vpravo se zapisuje rovnicí:
Součet setrvačné síly, tlumící síly a síly od pružiny se rovná budicí síle kmitající frekvencí ω. Z této rovnice získáme vztah pro amplitudu dynamické, tj. kmitavé, výchylky mechanického systému s jedním stupněm volnosti.
Vidíme, že tato amplituda dynamické výchylky vychází komplexní díky imaginární hodnotě tlumení, které představuje člen jCω. Dynamická poddajnost našeho jednoduchého modelu pak je:
kde jsme při úpravách použili tradiční symbol pro vlastní
frekvenci systému
Pro naše další úvahy je důležité, že vztah obsahuje pouze měřitelné konstanty tuhosti, hmotnosti a tlumení. K řešení stability obrábění podle [1] je potřeba pouze reálná složka komplexní dynamické poddajnosti, která se z rovnice (3) dá vypočítat opět jen algebraickými úpravami. Platí vztah:
ve kterém jsou opět jen měřitelné konstanty tuhosti, vlastní frekvence a tlumení. Jak je vidět, dynamická poddajnost je závislá na frekvenci budicí síly. Pro nulovou hodnotu frekvence, tj. pro statický případ, přechází dynamická poddajnost ve statickou 1/k. Důležité je si uvědomit, že G(ω) dává kladné hodnoty (a nulovou hodnotu) pokud je ω ≤ Ω a záporné hodnoty, pokud je ω ≥ Ω. Další podrobnosti nalezne zájemce např. v [4].
Statickou tuhost na nástroji lze změřit pomocí indikátorových hodinek a mincíře nebo závaží, případně s kladkou pro změnu směru. Je vhodné opakované zatěžování a uvolňování k vymezení vůle. Tlumení zjistíme poklepem na nástroj a záznamem vzniklých kmitů. Jelikož je ale známo, že průměrné tlumení frézovacích strojů se pohybuje v rozmezí 3 až 4 % z vlastní frekvence, můžeme tuto hodnotu použít a pak nám stačí k výpočtu dynamické poddajnosti již jen zjistit vlastní frekvenci.
Zde není situace vždy jednoduchá, pracujeme-li s nástroji větších průměrů. V tom případě se při obrábění rozkmitá nejen nástroj, ale i další části obráběcího stroje. Kmitavý systém pak sestává z těchto částí a jeho model je složitější. Znamená to, že stroj má několik vlastních frekvencí, které bychom museli určit.
Analýza takových případů je složitá. Kvůli jednoduchosti dalších úvah se proto omezíme na případy, kdy převažuje kmitání s jednou vlastní frekvencí. Potom i model stroje bude mít jednu vlastní frekvenci. To platí jen s malou odchylkou pro štíhlé nástroje s poměrem L:d větším než 2. Vlastní frekvenci lze pak určit spolehlivě poklepem na špičku nástroje v horizontální rovině a měřením dokmitu. Specializované měřicí přístroje ovšem mohou změřit reálnou i imaginární složku dynamické poddajnosti v závislosti na frekvenci a získaná data použít k další analýze stroje a procesu obrábění.
Naším cíle však není měření dynamických konstant ve vztahu (4). Chceme se vlastními silami a postupy dopracovat k informacím o možném výskytu kmitání při obrábění, kterému se v odborné literatuře říká samobuzené kmitání, anglicky nejčastěji „chatter“. Dříve však musíme vysvětlit co nejjednodušeji teorii stability při obrábění.
Princip teorie stability
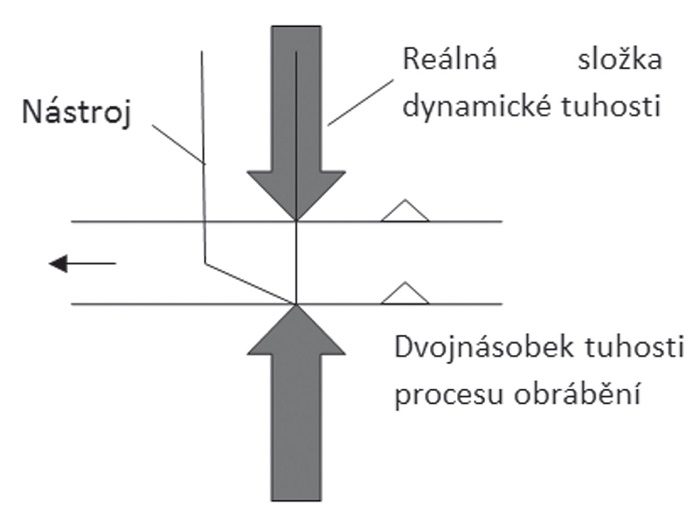
Obr. 3: Rovnováha tuhostí na mezi stability
Proces obrábění je možno si představit jako systém dvou pružin, pružiny systému stroje a pružiny řezného procesu. Spojení těchto pružin nese břit nástroje. Obě pružiny jsou charakterizovány tuhostí, která je definována jako poměr řezné síly k výchylce.
Představme si malou úchylku od ideálního povrchu – nerovnost, která mohla vzniknout házením rotujícího nástroje. Při příštím řezu způsobí tato nerovnost zvýšení řezné síly. Zvýšení bude malé, je -li proces poddajný, nebo větší, je -li proces tuhý. Toto zvýšení řezné síly deformuje systém stroje a nástroje, a protože je poddajnost stroje dynamická, dojde k rozkmitání nástroje. Na obráběném povrchu, mezi zuby frézy, vzniknou vlny, které se reprodukují při každém dalším řezu a rozkmitávají nástroj. Při určitém poměru tuhostí (poměr 2) zůstává velikost vln stejná – proces obrábění je na hranici stability (obr. 3). Proces je nestabilní, když se velikost vln při reprodukci zvětšuje. Když je proces stabilní, vlny se záběrem každého dalšího zubu zmenšují a mizí v následujících řezech. Kdybychom nerovnost přejížděli s velmi malou rychlostí, byl by to statický případ a nerovnost by pouze vychýlila nástroj a reprodukovala by se v následujícím řezu bez rozkmitání nástroje a vln na obrobku. Výsledky by neodpovídaly skutečnosti. Použití dynamické tuhosti, která zahrnuje vliv setrvačných sil a tlumení, vede k systému lobů nestabilního obrábění a mezer mezi loby, kde lze obrábět bez vibrací a s vyšší produktivitou. Umožnilo by také uvažovat vliv fázového posunutí. Je to podstatně dokonalejší, i když ještě ne dokonalé, řešení.
Nyní určíme tuhost procesu. Ta závisí na řezné síle, která je součinem specifického řezného odporu Kc a plochy řezu odebíraného materiálu, což je součin „ae“(radiální hloubka řezu) a „ap“ (axiální hloubka řezu).
Tuhost procesu je definována jako síla kolmá k vytvářenému povrchu dělená radiální hloubkou řezu ae.
Tuhost je vyšší pro obtížně obrobitelné materiály s vysokým řezným odporem. Je také vyšší pro větší axiální hloubku řezu.
Přepíšeme -li obr. 3 do rovnice tuhostí. Platí:
Převedením řezného odporu Kc na pravou stranu rovnice tuhostí (7) dostaneme formuli pro maximální hodnotu axiální hloubky řezu, která může být použita pro stabilní obrábění.
Teorie stability obrábění byla původně vyvinuta pro soustružení [1] a teprve později upravena pro frézování. Úpravy si vyžádaly určitá zjednodušení frézovacího procesu, která mohou způsobit další nepřesnosti. Princip však zůstává stejný.
Diagram stability
Diagram stability je závislost meze stability na otáčkách frézovacího nástroje. Mez stability je axiální hloubka řezu na mezi stability ap lim. Praxe ukazuje, že mez stability se mění s otáčkami nástroje. Kromě toho je mez stability závislá na dynamické poddajnosti systému stroj-nástroj-obrobek a také na specifickém řezném odporu materiálu obrobku, (8). Specifický řezný odpor Kc je ovlivněn částečně i geometrií nástroje, hlavně úhlem čela a sklonem šroubovice. Diagram vlastně odděluje od sebe oblasti se stabilními a nestabilními řeznými podmínkami. V rovnici (8) funkce G(ω)neg představuje negativní část reálné části dynamické poddajnosti systému stroj-nástroj-obrobek, tedy hodnoty pro ω ≥ Ω. Hodnoty ap lim vynášíme na svislou osu diagramu.
Na vodorovnou osu vynášíme otáčky podle vztahu:
kde frekvence f = ω/2π, písmeno z značí počet zubů nástroje, N je počet celých vln kmitů, které se vejdou mezi sousední zuby a ψ je necelá část vlny mezi zuby. Vztahy uvádíme jen proto, aby bylo zřejmé, jaké veličiny figurují v diagramu stability. My však usilujeme o dílenský postup určení diagramu stability, nikoli o jeho výpočet.
Diagram stability řeznou zkouškou
Diagram stability na obr. 4 je složen z lobů (z anglického „lobe“). Loby ukazují proměnlivost meze stability s otáčkami nástroje. Jejich zřetelnější tvar je vidět na obr. 5. V dílně si můžeme diagram stability „vyfrézovat“. Stačí k tomu stroj a nástroj i materiál obrobku, při jejichž použití se vyskytlo chvění. Nejsnazší a nejnázornější je frézovat drážky na mírně nakloněné rovině obrobku. Axiální hloubka řezu se bude plynule zvětšovat až do okamžiku, kdy se nástroj rozechvěje. Tím je dosaženo meze stability dle vzorce (8) při daných otáčkách dle vzorce (9). Diagram na obr. 4 byl vytvořen právě tímto způsobem. Vidíme na něm přibližně jeden a půl lobu.
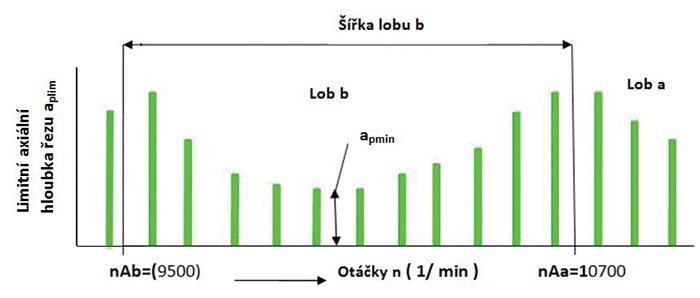
Obr. 4: Diagram stability pro jeden lob z řezné zkoušky
Z grafu jsou jasně patrné dvě oblasti. Zelené sloupce označují stabilní oblast řezných podmínek, nad nimi je oblast nestabilních podmínek, kde vzniknou vibrace. Vidíme, že mez stability je silně závislá na otáčkách nástroje. Ve střední části lobu je mez stability minimální, ale na hranicích lobu v okolí otáček 9 500 a 10700 1/min je naopak maximální, několikanásobně vyšší. Právě této závislosti lze využít pro zvýšení řezného výkonu nástroje.
Diagram na obr. 4 nezobrazuje celý rozsah otáček stroje a odpovídající počet lobů. To by bylo velmi pracné. Obsahuje však důležité oblasti dvou sousedních lobů a důležité parametry včetně ap min (minimální stabilní axiální hloubka řezu) a asymptoty dvou sousedních lobů a jejich otáčky. Asymptoty jsou vertikální přímky, ke kterým se nízko-otáčkové větve lobů přimykají, a které omezují šířku lobů. „Vyfrézovanou“ část diagramu stability použijeme nejprve k výpočtu vlastní frekvence kmitavého systému stroje, a tu dále využijeme k výpočtu řady otáček, na kterých leží další asymptoty lobů. Tím získáme rekonstruovaný diagram stability ve velkém rozsahu otáček, z něhož si můžeme vybrat dílčí rozsah vhodný pro naši aplikaci. Lépe nám to vysvětlí následující příklad.
Asymptoty lobů „a“ a „b“ byly odhadnuty na otáčkách nAa = 10 70 1/min a na otáčkách nAb = 9 500 1/min. Poloha asymptoty N-tého lobu se vypočte dle vzorce (10), dosadíme-li za frekvenci hodnotu vlastní frekvence, kterou označíme fn.
K určení vlastní frekvence však potřebujeme vypočítat tzv. Relativní šířky lobů. Postup je následující: Vzdálenosti mezi asymptotami sousedních lobů říkáme šířka lobu a je vyjádřena v otáčkách (1/min). Z naší zkoušky frézováním jsme určili pouze šířku lobu „b“:
Jestliže podělíme šířku lobu otáčkami asymptoty předchozího lobu, dostaneme Relativní šířku lobu. Numerická hodnota relativní šířky lobu „b“ z řezné zkoušky je 0,112.
Dosadíme -li do vztahu (12) výraz (10), ukáže se, že relativní šířka lobu nezávisí na vlastní frekvenci systému stroje ani na počtu zubů, závisí jen na čísle lobu. Připomeňme, že fyzikální význam čísla lobu je počet celých vln, který se při dané frekvenci kmitů, daných otáčkách nástroje a počtu zubů vejde do mezery mezi sousedními zuby. Podle počtu vln se pak loby číslují.
Vidíme, že relativní šířka lobu je univerzální hodnota řady celých čísel N nezávislá na kmitavém systému i na nástroji. Hodnoty jsou vypočteny v tab. 1 pro N = 2 až 11.
Tab. 1
Číslo lobu= počet vln mezi zuby |
2 | 3 | 4 | 5 | 6 | 7 | 8 | 9 | 10 | 11 |
RWlb | 0,500 | 0,333 | 0,250 | 0,200 | 0,167 | 0,143 | 0,125 | 0,111 | 0,100 | 0,091 |
Jednoduché srovnání hodnot RWlb v tabulce s výsledkem (12) ukazuje, že lob „b“ je lob číslo 9 (N = 9) a lob „a“ je lob číslo 8.
Nyní je možno vypočítat vlastní frekvenci kmitavého systému stroje z rovnice (10) pro známý počet zubů frézy, což umožní rekonstrukci diagramu stability pro velký rozsah otáček. V našem příkladu na obr. 4 vychází vlastní frekvence systému stroje:
Průměrná hodnota fn = 4277,5 Hz
Pozice dalších asymptot lobů na otáčkové ose vypočteme ze vztahu (10). Dostaneme řadu otáček, v jejichž okolí je mez stability zvýšená, jak ukazuje už obr. 4. Vypočtené otáčky pro náš příklad jsou uvedeny v tab. 2 spolu s příslušným číslem lobu N. Rozsah otáček byl omezen tak, aby vycházela realistická řezná rychlost pro nástroj průměru 20 mm a běžné případy frézování. Pro zvláštní aplikace lze dopočítat polohy asymptot pro libovolné N. Rekonstruovaný diagram stability je uveden na obr. 5.
Tab. 2
N | 1 | 2 | 3 | 4 | 5 | 6 | 7 | ||
Otáčky nAN | 85 550 | 42 775 | 28 516 | 21 387 | 17 110 | 14 258 | 12 221 | ||
N | 8 | 9 | 10 | 11 | 12 | 13 | 14 | ||
Otáčky nAN | 10 693 | 9 505 | 8 555 | 7 777 | 7 129 | 6 581 | 6 111 | ||
Řezná rychlost [m/min]. Nástroj D = 20 mm. Řada N = 8 až 14 |
672 | 597 | 537 | 488 | 448 | 413 | 384 |
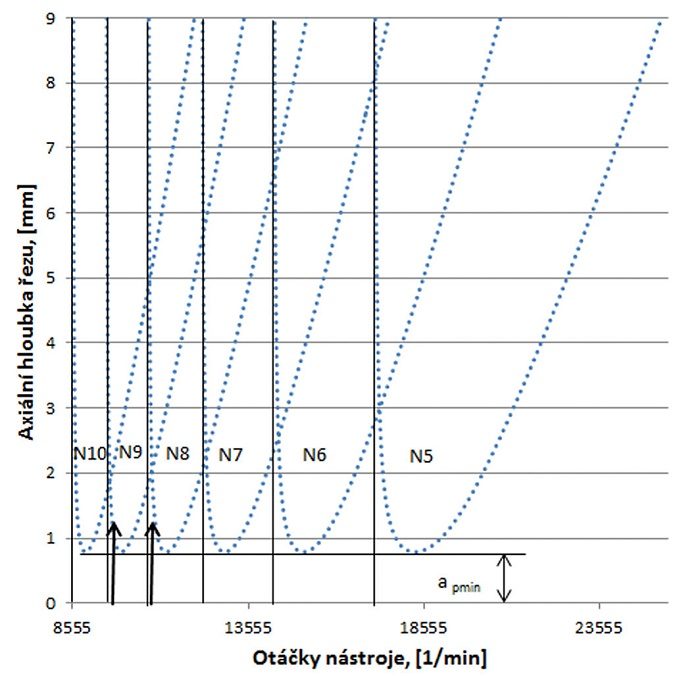
Obr. 5: Diagram stability rekonstruovaný
V diagramu vidíme, že s nárůstem otáček se rozšiřují a zvyšují mezery stabilních řezných podmínek mezi loby. Největší možnosti zvýšit produktivitu tedy existují vždy v okolí asymptot s nízkými čísly lobů. Odpovídající otáčky vřetena jsou ale vysoké a mohou být omezeny konstrukcí vřetena. Druhým limitem využití vysokých otáček může být řezná rychlost, a to jak ze strany materiálu a průměru nástroje, tak ze strany materiálu obrobku. Silné šipky ukazují rozsah otáček, ve kterém bylo frézováno a měřena mez stability dle obr. 4.
S klesajícími otáčkami se mezery mezi asymptotami zužují a oblasti stabilního obrábění se zmenšují. Je tedy možné očekávat podstatné zvýšení řezného výkonu v oblasti vysokých otáček nebo řezných rychlostí, které se používají při frézování slitin hliníku nebo při použití malých průměrů fréz. Chceme -li na stroji obrábět např. slitiny hliníku, nebudeme zkoušet řezné rychlosti 900 m/min. S nástrojem o průměru 16 mm tomu odpovídají otáčky 18 000 1/min, kde vidíme v diagramu, že stabilní hloubka řezu je menší než 1 mm, ale použijeme otáčky v okolí 21 380 1/min nebo otáčky 17 100 1/min, kde je naopak stabilní hloubka řezu vysoká, až 3 mm. Tečkované hranice stability představují ideální, modelový případ, který nemusí řezná zkouška potvrdit. Proto při volbě řezných podmínek raději udržujeme určitý odstup (např. 20 %) od těchto křivek. Změna obráběného materiálu znamená podle teorie pouze procentuální změny vertikálních hodnot podle převrácené hodnoty řezného odporu. Hodnoty řezného odporu pro řadu běžných obráběných materiálů uvádí např. firma Sandvik ve svém katalogu, včetně vlivu střední tloušťky třísky. Pro uhlíkovou ocel je orientační hodnota Kc = 2 200 MPA, pro slitiny hliníku Kc = 880 MPA. Při zvyšování výkonu obrábění je nutno kontrolovat výkon motoru vřetene, který se může také stát limitujícím faktorem.
Loby mohou být rekonstruovány pouze na základě teorie, která však, jako každý model, se od skutečnosti nutně odchyluje. Na odchylkách se podílí např. odhad polohy asymptot ve „vyfrézovaném“ diagramu stability. Stabilní řezné podmínky mohou být přesně určeny jen řeznou zkouškou a teoretické loby jsou na obr. 5 jen kvůli názornému vymezení pravděpodobných oblastí stabilních řezných podmínek. Možná, že rekonstrukce lobů není nutná a že bylo lépe zaměřit řezné zkoušky na blízké okolí asymptot v oblasti technologicky zajímavých otáček, kde lze očekávat největší zvýšení výkonu obrábění.
Zajímavá je také oblast nízkých řezných rychlostí asi pod 40 m/min a nižší, [2], [3]. Tato oblast zatím ještě nemá teoretické řešení, ale je dobře známá v praxi a dokumentována experimentálně. Teorie jen navrhuje pravděpodobný mechanismus tohoto jevu. Předpokládá se, že působí tak zvané procesní tlumení dotykem hřbetu nástroje s vlnami o zmenšující se délce, ačkoliv stopy kontaktu nebyly nikdy zjištěny.
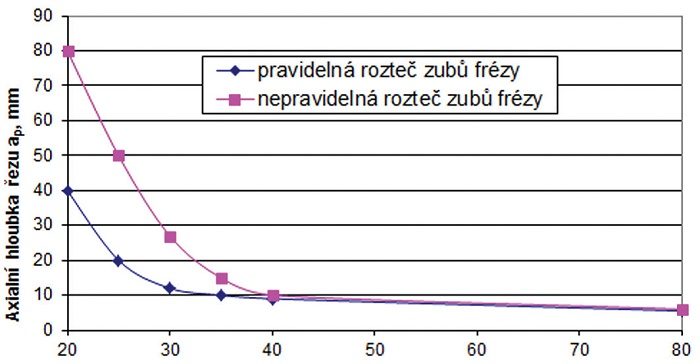
Obr. 6: Meze stability při frézování titanové slitiny nízkými řeznými rychlostmi
Praktické zkušenosti však ukazují, že omezující axiální hloubka řezu při frézování v této oblasti roste přibližně exponenciálně se snižováním řezné rychlosti. Křivky na obrázku 6 jsou obálky nejmenších hodnot lobů získaných z řezných zkoušek. Protože titan a slitiny niklu je stejně výhodné obrábět za nižších rychlostí, je vhodné experimentálně prozkoumat tuto oblast. Zajímavá je značně vyšší výkonnost fréz s nepravidelnou roztečí zubů.
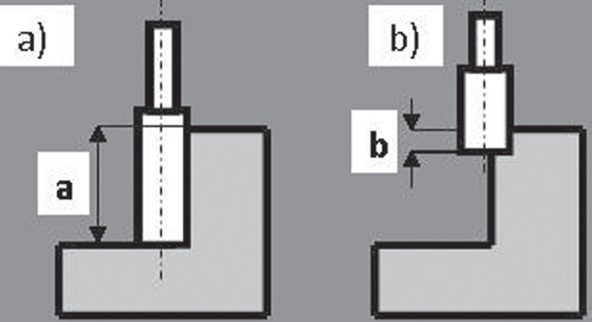
Obr. 7
Vyšší mez stability nezajistí, ale jen umožní, vyšší produktivitu. Je nutno vybrat obrobky, které se dají obrábět větší axiální hloubkou řezu, jako například letecké součásti s hlubokými odlehčovacími kapsami, hluboké zápustky a podobně. Obr. 7 ukazuje rozdíly při obrábění s velkou a malou axiální hloubkou řezu. S větší hloubkou řezu se zvýší produktivita, využije se lépe délka aktivního břitu. Je ale nutné výkonnější chlazení celého břitu pro zachování životnosti nástroje.
Jsou různé způsoby, jak zlepšit stabilitu a vyhnout se samobuzeným kmitům v celém rozsahu používaných řezných rychlostí. Patří mezi ně použití nástrojů s nepravidelnou roztečí zubů nebo s nepravidelným stoupáním šroubovice. Některé stroje jsou také vybaveny cykly změny otáček. Tyto metody nejsou v uvedené teorii zahrnuty, ale řezné zkoušky by ukázaly jejich výhody. Viz např. obr. 6, kde jsou porovnány nejvyšší stabilní hloubky řezu pro nástroj s pravidelnou a s nepravidelnou roztečí.
Obrábění s velkou hloubkou řezu je jediný způsob zvýšení produktivity, který nemá za následek snížení životnosti nástroje, protože prodlouží využívanou délku ostří, takže zatížení ostří na jednotku délky se nemění. Zvyšování produktivity, na příklad zvyšováním řezné rychlosti, přináší významné snížení životnosti nástrojů.
Závěr
V tomto článku jsme navázali na článek s titulem „Využití teorie samobuzených kmitů ke zvýšení produktivity a kvality obrábění“, publikovaném v magazínu machining & tooling 3-2015, [5], kde jsme poukázali na dosud nevyužité možnosti zvýšení produktivity frézování. V tomto novém zpracování stejného tématu jsme se zabývali praktickým způsobem, jak přímo v dílně získat informace o dynamickém chování stroje a nástroje při frézování. Zaměřili jsme se na metodu, která umožňuje několika zkouškami frézováním v omezeném otáčkovém rozsahu stanovit přibližně vlastní frekvenci systému stroj -nástroj, a tu pak použít k určení oblastí stabilních řezných podmínek v celém otáčkovém rozsahu stroje. Jelikož při výkonném obrábění často vznikají vibrace, které poškozují obrobek i nástroj, je výhodné znát způsoby, jak se těmto jevům vyhnout. Využití diagramu stability je jednou z možností, kterou může použít každý technolog.
Literatura
[1] Poláček M., Výpočet stability rámu obráběcího stroje. Kandidátská disertační práce, ČVUT v Praze, 1955.
[2] Bach P., Trmal G. J., Váňa J., Malý J., High Performance Titanium Milling at Low Speed, Proceedings CIRP Fifth Conference on HPC, 2012, Vol. 1, p. 226–231.
[3] Bach P., Drobílek J., Obrábění za nízkých řezných rychlostí, machining & tooling magazine, 3-2012.
[4] Bach P., Vibrace při obrábění, machining & tooling magazine, 1-2013.
[5] Trmal J. G., Bach P., Využití teorie samobuzených kmitů ke zvýšení produktivity a kvality obrábění, machining & tooling magazine, 3-2015, str. 54–56.
Dr. Ing. Jiří George Trmal
University of the West of England, Bristol, emeritní výzkumný pracovník
www.uwe.ac.uk
Ing. Miroslav Janota, Ph.D.; doc. Ing. Pavel Bach, CSc.
ČVUT v Praze, Výzkumné centrum pro strojírenskou techniku a technologii
www.rcmt.cvut.cz
Mohlo by se Vám líbit
Cílem je stát se jedničkou pro oblast kabelů
- Elektro
-
10. července 2025
Společnost KONEKA, která vznikla vloni na podzim jako dceřiná společnost PRAKAB (PRAKAB Pražská Kabelovna s.r.o.), plánuje v letošním roce dále rozšiřovat své služby a produktové portfolio. […]
Každý den je jinak BAREVNÝ!
- Plasty
-
08. července 2025
Chcete si pověsit na zeď něco barevného a užitečného? Připravili jsme pro Vás nový plakát se základními informacemi o barevném prostoru CIELab a výpočty ΔE […]
Nové elektrické polohovací zařízení HIWIN: Spolehlivý a přesný lineární pohyb
- Automotive
-
08. července 2025
Jedinečné na trhu díky přídavnému podpůrnému vedení HIWIN, přední výrobce lineárního vedení, kuličkových šroubů a polohovacích zařízení, představil na letošním veletrhu Automatica 2025 v Mnichově […]