19. listopadu 2018 18:08
FINAL Tools Obrábění velmi přesných děr na světové úrovni! (2. část)
Zúročil jste nějak svou zkušenost ze Škodovky?
Ano, chtěl jsem se dostat do zahraničí a to, co ve Škodovce fungovalo, jsem po dvou letech zúročil ve firmě OPEL – General Motors ve Vídni. To byla tehdy třetí největší motorárna na světě, s produkcí asi 1 milion motorů ročně. Dostali jsme tam náš informační leták přes známého, který prodával auta blízko zmiňované motorárny. Nečekal jsem, že by někdo na ten leták zareagoval, že by si ho vůbec někdo všiml. Ale za 14 dnů přišla poptávka, jestli bych nemohl dojet, že mají obrovské problémy přesně v tom, co jsem popsal v letáku a co jsem znal ze Škodovky. Mluvil jsem jim z duše, protože tyto problémy byly nakonec v celém světě stejné, jedno jestli to byla Škodovka, OPEL nebo Fiat. Opel bylo velké sousto, ale opět jsme měli technické výsledky a pak nikoho nezajímalo, jestli jsme garážová nebo světová firma. Mistři ve výrobě o nás měli velký zájem a říkali nám, že takto se můžeme dostat dál do Opelu v Německu a do celé Evropy.
V tu dobu za mnou přišel nějaký člověk v zastoupení pana Maiera z německé firmy HAM – Hartmetallwerkzeugfabrik Andreas Maier a řekl mi, že mě sleduje, že ví, jaké máme úspěchy. Oni že takové nástroje také testují, ale takové úspěchy nemají, jestli by nebylo rozumnější založit s nimi společnou firmu. Oni by produkty dodávali do celého světa, zastupovali by nás a my bychom se zabývali vývojem a výrobou. Znělo to jak v pohádce, jako ideál. Proč bych jezdil po světě a jazykově se trápil třeba ve Švýcarsku nebo v Itálii, kde jsem již navštívil automobilky Ferrari a Fiat. Věděl jsem, že problém s obráběním je skutečně všude stejný a šlo o komunikaci a obchod. Na to konto jsem během tří měsíců s panem Maierem založil firmu HAM-FINAL. Přistoupil jsem na jeho majoritní podíl, protože firma měla obchodní zastoupení po celém světě a čekal se přínos pro obě strany. Přestože firma HAM měla 380 pracovníků, tak se ukázalo, že nikdo z jejich techniků nebyl schopen se mnou spolupracovat ve specializaci, kterou jsem se zabýval já. Po skoro 20 letech koexistence a poté, co pan Maier zemřel, jsem se s rodinou domluvil, že většinový podíl pana Maiera odkoupím zpět. Bylo to dlouhé jednání, ale po dvou letech jsem získal opět 100% podíl ve firmě. Jenže uběhlo 20 roků a veškeré aktivity pro zahraničí jsem měl v té době zablokované, neboť oni byli výhradními prodejci našich nástrojů na světových trzích. Přesto FINAL Tools je i nadále jediným dodavatelem výstružníků ∅ 5 mm pro vystružování vodítek ventilů v hlavách motorů v OPEL GM v Rakousku. Za toto období nás nikdo ze světových výrobců nevytlačil žádným lepším řešením.
Takže jste se jako firma profilovali jako specialista na výrobu přesných děr.
Ano, je to velmi úzká specializace. Když si pro srovnání vezmete katalog Hoffmanna, který má více než 1 000 stran, tak naše nástroje, které vyrábíme, jsou jenom na 2 až 3 stránkách. Tím se vlastně zabýváme jako firma dvacet let, já profesně už čtyřicet let. Ale výroba přesných děr není jen provrtaná díra, ale následně její plocha velmi přesně válcovitě nebo kuželovitě opracovaná s různými vnitřními tvary, např. nábojová komora u zbraní. Uplatnění našich inovačních nástrojů je třeba v nástrojárnách při opravě forem. Vyhazovač ve formě opotřebí otvor a ten se musí znovu obrobit – vybrousit. My jsme přišli s řešením, že se tyto otvory nemusí vybrušovat, ale mohou se vystružovat na vyvrtávacím stroji. První nástrojárna, kde jsme zavedli takovou technologii, byla v Modřicích. Vybrušování takové formy jsme z nějakých 28–32 hodin zaměnili za obrábění za méně než za 8 hodin. No a druhá nástrojárna byla Mladá Boleslav, jedna z největších nástrojáren v České republice. Zde to byla i otázka nákupu kvalitních obráběcích center. Když jsme tam začínali, vyráběli na starých strojích, které byly neefektivní. V nástrojárně investovali 100 milionů do obráběcích center. Problém ale byl s obsluhou. Konvenční stroje obsluhovali pracovníci, kteří absolutně neměli a nemohli mít znalost CNC techniky. Neměli chuť se učit novou technologii, bojkotovali výrobu, báli se, že je CNC stroje nahradí. Chtěli si udržet řemeslo. Uměli si spočítat, že co se obrábí za hodinu, půjde najednou za 3 minuty. Ale co pak s obsluhou? Takže mě zase trvalo víc jak rok, kdy jsem tam jezdil a nástroje předváděl a zkoušel. Postupem času jsme zavedli nové nástroje do celé nástrojárny, kde se úspěšně používají doposud.
Současnost je tedy jaká?
Teď je situace taková, že máme nové programy. Od automobilek pomalu odcházíme, řada patentů měla platnost 20 let a doba již uběhla. Myslím, že návrat do automobilek je těžký. Obnovovat patenty v situaci, kdy silní giganti, kteří dneska na trhu jsou, by to dokázali velmi rychle zajistit, jak výrobně, obchodně, tak servisem atd. To je velké riziko. Tudíž tady šanci moc nemáme. Proto se orientujeme na firmy, které vyrábí hydraulické komponenty. Zde je řada přesných otvorů a tím prostor pro naše technologická řešení. Nejpřesnější otvory se vyrábí tak, že se na jednom stroji otvor vyvrtá a vystruží a pak otvory dokončí honovací stroj s přesností asi 10 mikronů tvarové a rozměrové přesnosti. Nyní je obrovský trend Průmysl 4.0. Pokud chce někdo vyrábět a automatizovat výrobu hydraulických komponentů, tak musí řešit obrovskou souvislost výsledného obrobku na nástroj. Jestli je stroj a nástroj spolehlivý, můžete spustit výrobu a přijít třeba za tři dny. Tak se to dělá u plně robotizovaných výrob. Zde musí jít všechno samo a na 100 % spolehlivě. Ale ukazuje se, že u těch komponentů, kde jsou otvory s přesností do 10 mikronů, je problematická návaznost obráběcího a honovacího stroje v rámci propojeného robotizovaného pracoviště. Proto je velká snaha těchto přesností dosáhnout už na obráběcích centrech, a to se často nedaří. Ale výrobní firmy do automatizace jít musí. Zde je místo pro nás. Nyní nás oslovila v Itálii pobočka firmy Poclain. V Poclainu jsme zavedená firma. Už několik let dodáváme do poboček ve Francii a Indii. Poclain potřebuje vyrobit nástroje pro přesné obrobení hydraulických rozvaděčů. Pořídili stroj odhadem za 40 milionů korun do plně robotizovaného pracoviště. Tento stroj má velké prostoje, protože nedokáže s žádným světovým nástrojem dosáhnout požadované přesnosti. Zkoušeli to už tři největší dodavatelé těchto nástrojů, ale ani jeden neuspěl tak, aby stroj jel bez dozoru a aby produkoval v požadované přesnosti. Stroj má kontrolní měření a pokud obrobek není v toleranci, tak se výroba zastaví. My se nyní zabýváme vývojem těchto důležitých nástrojů.
Problém může být ve stroji, v nástroji nebo v obojím. Když ale někdo dodává stroj za 40 milionů, tak musí klientovi říct: ta výroba je odladěná a s tímto nástrojem to bude fungovat, nebo se pletu?
Ano, máte úplně pravdu. My jsme se ptali, jak jste mohli koupit stroj, když garantem funkčnosti technologie není výrobce stroje? Kdyby si někdo objednal stroj s požadavkem výroby určitého obrobku a s podmínkou dodání s technologií se vším všudy, tak by samozřejmě výrobce stroje musel garantovat i to, že stroj bude produkovat. Jinak na sebe bere veliké riziko. Ztráty, které vznikají, když mašina nejede, jsou obrovské. Ale údajně to bylo dané tak, že objednavatelé jim dodali technologii, která byla závislá na lidském faktoru, což u robotizovaného stroje nejde akceptovat. Výrobce stroje se nezabýval tím, jaké nástroje se budou používat. Podařilo se to pouze částečně, stroj fungoval dobře, ale jeden jediný nástroj – dokončovací, nebyl schopen zajistit otvor v takové přesnosti, aby mohli pokračovat dál. Tzn. nedosáhlo se kvalitního povrchu, tvarové přesnosti, přímosti otvoru atd. Je to náročný obrobek a sleduje se spousta parametrů, které když se nedosáhnou, tak tento výrobek nemůže plnit funkci. Třeba na bagru je hydraulický rozvaděč – regulátor. Ten přepouští pomocí pístů hydraulický olej do jednotlivých hydromotorů. To se vše testuje na zkušebně, kde se systém natlakuje a zkouší se průnik kapaliny. Pokud díry nemají tvarové přesnosti a únik kapaliny je větší než přípustná hodnota, tak se do bagru nenamontuje, protože by to způsobovalo chyby ve funkci. Něco se dá ještě opravit, například vyměnit píst nebo znovu obrobit díru. Takto byla výroba odladěná a fungovala. Jenže s přechodem na robotizovaný stroj bez vlivu lidského faktoru se zjistilo, že nejdou využít všechny dosud používané nástroje a metody výroby. Nyní do toho vstupujeme my. Začínáme vyrábět nástroje naší koncepce a říkáme: „S našimi nástroji dokážete na obráběcím centru vyrábět tak přesně, jak jste předtím museli na jednom centru obrobit a na druhém stroji dokončit.“ A to je trend: pokud máte kvalitní stroj a nástroj, tak můžete vyřadit honovací stroj a vyrábět pouze jedním strojem. Taková výroba se pak jednoduše robotizuje.
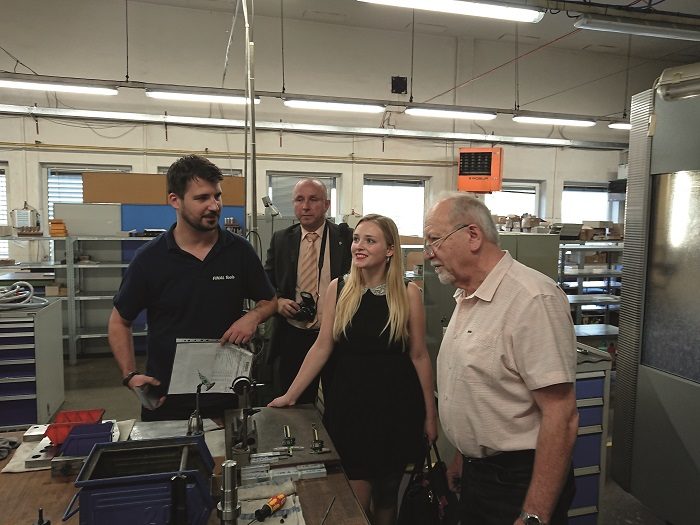
Naše redakce při prohlídce výroby s panem Fialou a referentem obchodu a controllingu, panem Ing. Jozefem Šakem
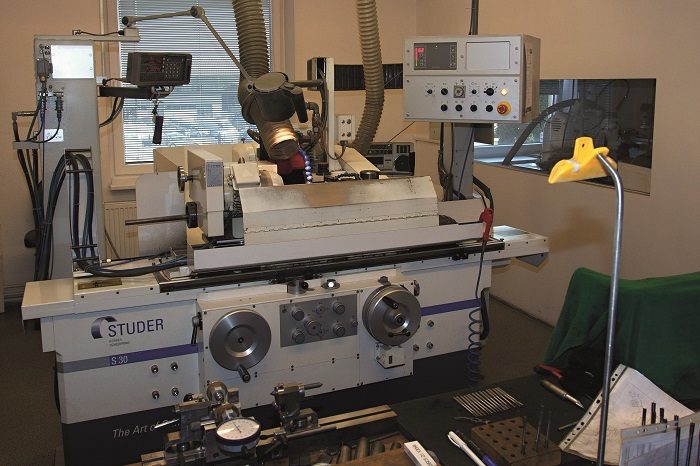
Broušení nástrojů s břity ze slinutých karbidů a diamantů probíhá na samostatném klimatizovaném pracovišti
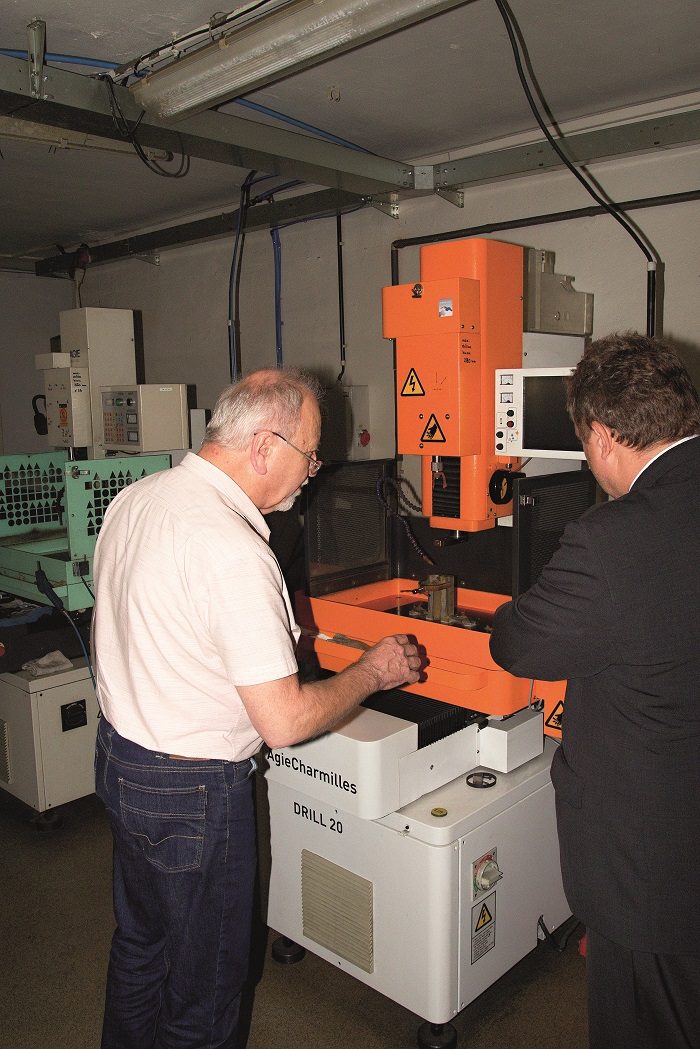
AgieCharmilles DRILL 20 určená k vrtání otvorů v nástrojích ze slinutých karbidů
1. část rozhovoru: https://nastrojarna.oneindustry.one/final-tools-obrabeni-velmi-presnych-der-na-svetove-urovni-1-cast/
Pokračování 3. části rozhovoru: https://nastrojarna.oneindustry.one/final-tools-obrabeni-velmi-presnych-der-na-svetove-urovni-3-cast/
Mohlo by se Vám líbit
Nová vlajková loď generátorů libovolných průběhů s šířkou pásma 3,9 GHz a výstupní rychlostí 10 GS/s
- Elektro
-
12. července 2025
Společnost Spectrum Instrumentation představuje čtyři nové vysoce výkonné generátory libovolných průběhů (AWG), které jsou významným milníkem v nabídce jejích produktů. Nové generátory AWG jsou určené […]
Cílem je stát se jedničkou pro oblast kabelů
- Elektro
-
10. července 2025
Společnost KONEKA, která vznikla vloni na podzim jako dceřiná společnost PRAKAB (PRAKAB Pražská Kabelovna s.r.o.), plánuje v letošním roce dále rozšiřovat své služby a produktové portfolio. […]
Každý den je jinak BAREVNÝ!
- Plasty
-
08. července 2025
Chcete si pověsit na zeď něco barevného a užitečného? Připravili jsme pro Vás nový plakát se základními informacemi o barevném prostoru CIELab a výpočty ΔE […]